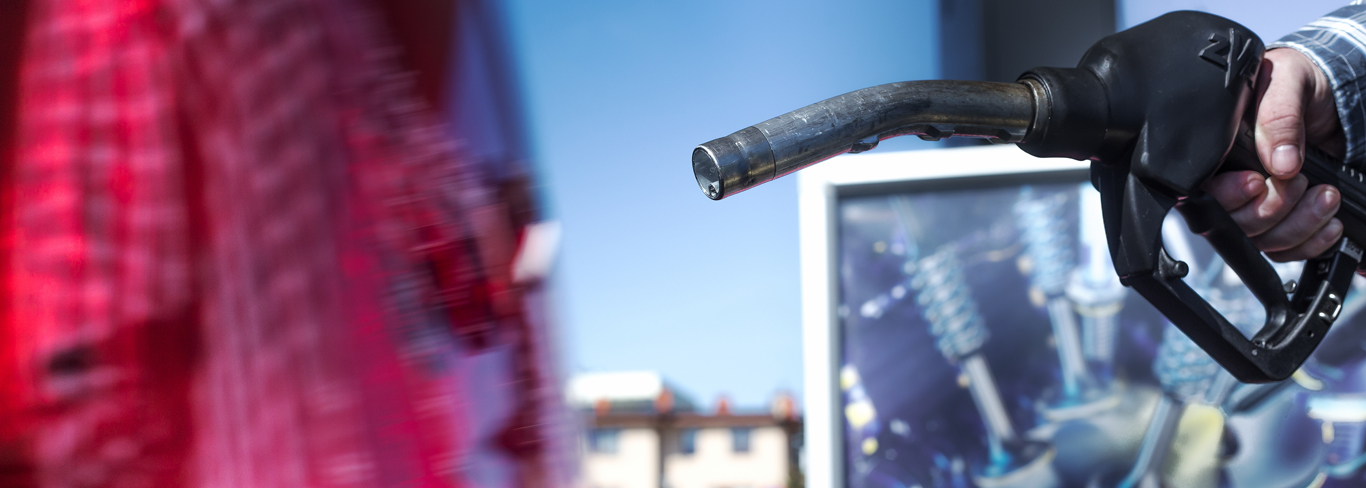
FEEDSTOCKS AND PRODUCTION PROCESSES
In its refining and petrochemical operations, the Group processes various raw materials and semi-finished products. Crude oil is the principal raw material used in production, and other feedstocks include biocomponents and chemicals.
Consumption of raw and other materials
Non-renewable raw materials [t]
|
PKN ORLEN |
ORLEN Lietuva |
Unipetrol |
|||
2020 |
2019 |
2020 |
2019 |
2020 |
2019 |
|
Crude oil |
15,305,739 |
16,207,406 |
7,847,448 |
9,515,218 |
6,075,865 |
7,853,987 |
Other |
1,884,392 |
2,059,879 |
389,255 |
374,864 |
2,005,919 |
2,282,514 |
Renewable raw materials [t]
|
PKN ORLEN |
ORLEN Lietuva |
Unipetrol |
|||
2020 |
2019 |
2020 |
2019 |
2020 |
2019 |
|
Biocomponents |
732,079 |
828,661 |
105,434 |
92,127 |
277,040 |
293,720 |
Crude oil consumption
|
Crude oil consumption [t] |
Share of crude in total feedstocks [%] |
||
2020 |
2019 |
2020 |
2019 |
|
PKN ORLEN |
15,305,739 |
16,207,406 |
83% |
83% |
ORLEN Lietuva |
7,847,448 |
9,515,218 |
96% |
97% |
Unipetrol |
6,075,865 |
7,853,987 |
77% |
79% |
Crude oil, a non-renewable resource, is purchased for all ORLEN Group refineries as part of an integrated procurement process handled by PKN ORLEN, which buys oil from external suppliers.
Other materials used in our plants include natural gas, biocomponents and semi-finished products, exchanged mainly between the refinery and the petrochemical plants (they are not primary feedstock).
Consumption of biofuels meeting the sustainability criteria
In order to protect the environment and in view of the national requirements to ensure the mandatory minimum share of biofuels in transport, in 2020 the ORLEN Group used over 765,000 tonnes of methyl esters, around 243,000 tonnes of bioethanol and almost 31,000 tonnes of synthetic bio-hydrocarbons. All the biofuels used by the ORLEN Group in its markets met the sustainability criteria specified in the RES Directive and Fuel Quality Directive.
All the biofuels used by the ORLEN Group in its markets met the sustainability criteria specified in the RES Directive and Fuel Quality Directive.
Volumes of biofuels used by the ORLEN Group – biofuels meeting the sustainability criteria on the Polish, Czech and Lithuanian markets
|
2020 |
2019 |
2020 |
2019 |
2020 |
2019 |
2020 |
2019 |
Poland* |
Poland* |
Czech Republic** |
Czech Republic** |
Lithuania*** |
Lithuania*** |
TOTAL |
TOTAL |
|
Esters (t) |
570,435 |
642,684 |
126,190 |
141,205 |
68,695 |
68,869 |
765,320 |
852,758 |
of which: produced by ORLEN Południe [t] |
239,793 |
256,043 |
- |
- |
- |
- |
239,793 |
256,043 |
Bioethanol [t] |
166,731 |
191,832 |
46,270 |
50,773 |
30,092 |
21,570 |
243,093 |
264,175 |
Synthetic hydrocarbons for diesel oil – HVO [t] |
- |
997 |
21,310 |
- |
6,639 |
1,688 |
27,949 |
2,685 |
Synthetic hydrocarbons for diesel oil – co-HVO [t] |
2,060 |
- |
135 |
- |
727 |
- |
2,922 |
- |
Synthetic hydrocarbons for gasoline [t] |
- |
233 |
- |
- |
- |
- |
- |
233 |
|
||||||||
|
2020 |
2019 |
2020 |
2019 |
2020 |
2019 |
2020 |
2019 |
Poland* |
Poland* |
Czech Republic** |
Czech Republic** |
Lithuania*** |
Lithuania*** |
TOTAL |
TOTAL |
|
Esters [m3] |
639,578 |
720,498 |
142,911 |
159,915 |
77,797 |
77,994 |
860,286 |
958,407 |
of which: produced by ORLEN Południe [m3] |
268,826 |
287,044 |
- |
- |
- |
- |
268 826 |
287,044 |
Bioethanol [m3] |
214,369 |
246,571 |
58,275 |
64,188 |
38,043 |
27,269 |
310,687 |
338,029 |
Synthetic hydrocarbons for diesel oil – HVO [m3] |
- |
1,291 |
27,321 |
- |
8,522 |
2,167 |
35,843 |
3,458 |
Synthetic hydrocarbons for diesel oil – co-HVO [m3] |
2,666 |
- |
174 |
- |
875 |
- |
3,715 |
- |
Synthetic hydrocarbons for benzene [m3] |
- |
302 |
- |
- |
- |
- |
- |
302 |
Note: Biocomponents not produced by ORLEN Południewere purchased from third-party suppliers.
* To maintain consistency with the NIT report to the Energy Regulatory Office, the conversion of tonnes into thousands of litres for PKN ORLEN S.A. was based on densities calculated in accordance with the Minister of Economy’s Regulation on heating values of biocomponents and liquid fuels of October 21st 2014. For the Czech Republic and Lithuania, standard densities were used.
** Biocomponents used for blending fuels for the Czech market.
*** Biocomponents marketed on the Lithuanian, Latvian and Estonian markets.
Benzene, lead and sulfur content in fuels
The key function of the ORLEN Group refinery is to produce liquid fuels meeting the applicable regulatory requirements and technical standards. All processes along the production chain are designed to obtain high-quality fuel components to be processed into fuels meeting the applicable requirements.
The benzene, lead and sulfur content in liquid fuels, by Group company, is presented in the TABLE.
PKN ORLEN, Production Plant in Płock
Crude oil is separated into fractions (distillates) in fractional distillation units.
At subsequent stages, the distillates are further processed in:
- Cracking unit,
- Alkylation unit,
- Reforming unit,
- Isomerisation unit,
- Diesel fuel hydrodesulfurisation unit,
- Hydrocracking unit and
- Petroleum tar hydrodesulfurisation unit,
where the following processes occur: hydrogenation, conversion of nitrogen and oxygen compounds, cracking of paraffin, olefinic and aromatic hydrocarbons with side chains into hydrocarbons having lower molecular mass, conversion of low-octane C5-C6 aliphatic hydrocarbons into higher-octane isomers, dearomatisation, and demetallisation.
Also, sulfur and benzene are removed to achieve concentration levels ensuring the components meet the required quality standards. The fuel components do not contain lead.
Liquid fuels are made by blending selected components (including biocomponents in the case of some fuel types) and adding boosters and additives according to a blending formula.
ORLEN POŁUDNIE
The main purpose of the plant is to produce biodiesel (fatty acid methyl esters; FAMEs).
The key steps in FAME production include:
- Chemical degumming,
- Continuous refining,
- Esterification of fatty acids,
- Transesterification of rapeseed oil and
- Washing and drying of biodiesel,
during which the following processes occur: removal of phosphorus compounds and free fatty acids from rapeseed oil, reduction of acidity, reacting oil with methanol to form methyl esters, biodiesel washing and drying. There is no need for desulfurisation or benzene and lead removal processes.
.jpg)
ORLEN Lietuva
Crude oil is separated into fractions (distillates) in fractional distillation units.
At subsequent stages, the distillates are further processed in:
- Cracking unit,
- Reforming unit,
- Isomerisation unit,
- Visbreaking unit,
- Oligomerisation unit and
- Diesel fuel hydrodesulfurisation unit,
where the following processes occur: hydrogenation, conversion of nitrogen and oxygen compounds, cracking of paraffin, olefinic and aromatic hydrocarbons with side chains into hydrocarbons having lower molecular mass, conversion of low-octane C5-C6 aliphatic hydrocarbons into higher-octane isomers, dearomatisation, and demetallisation.
Also, sulfur, benzene and lead are removed to achieve concentration levels ensuring the components meet the required quality standards.
Liquid fuels are made by blending appropriate components (including biocomponents in the case of some fuel types) and adding boosters and additives in accordance with a blending formula.
UNIPETROL RPA – Litvínov and Kralupy refineries
Crude oil is separated into fractions (distillates) in fractional distillation units.
At subsequent stages, the distillates are further processed in:
- Cracking unit,
- Reforming unit,
- Isomerisation unit,
- Diesel fuel hydrodesulfurisation unit,
- Hydrocracking unit and
- Visbreaking unit,
where the following processes occur: hydrogenation, conversion of nitrogen and oxygen compounds, cracking of paraffin, olefinic and aromatic hydrocarbons with side chains into hydrocarbons having lower molecular mass, conversion of low-octane C5-C6 aliphatic hydrocarbons into higher-octane isomers, dearomatisation, and demetallisation.
Also, sulfur and benzene are removed to achieve concentration levels ensuring the components meet the required quality standards. The fuel components do not contain lead.
Liquid fuels are made by blending selected components (including biocomponents in the case of some fuel types) and adding boosters and additives according to a blending formula.
In order to meet the environmental requirements, biocomponents characterised by lower CO2 emissions are used in the processes.
Productand service labelling
The obligations of the ORLEN Group companies to provide information on potential hazards associated with the chemicals they manufacture or import follow from international and EU laws. The scope and division of responsibilities at the Group companies are defined in internal regulations.
Safety data sheets, developed in accordance with the REACH Regulation, are the basic source of information on the classification and hazards for the chemicals manufactured or imported by the ORLEN Group companies. Products are classified based on research and expert knowledge of their properties, and the classification makes it possible to label them correctly (in accordance with the CLP Regulation) and identify risks in transport, based on which the dispatchers prepare the ADR labels (hazard warning labels). Safety data sheets are mainly a source of information on products intended for industrial and professional applications. In the case of products marketed directly for use by general consumers, the relevant information is provided by ORLEN Group companies by appropriate labelling of product packaging. In addition to pictograms, labels on product packaging contain appropriate hazard and precautionary statements (H and P statements). Given the wide range of applications of ORLEN Group products, information on product packaging is supplemented with detailed data required under specific legal provisions applicable to detergents, fertilizers, etc.
Starting from January 1st 2021, ORLEN Group companies will be obliged to notify hazardous mixtures to Poison Centres in accordance with the provisions and deadlines set out in Annex VIII of the CLP Regulation. Such notifications will be made through an IT tool developed by the European Chemicals Agency (ECHA). To make a notification, a UFI code will have to be generated for each mixture. The UFI code will then be placed on the packaging or/and safety data sheet.