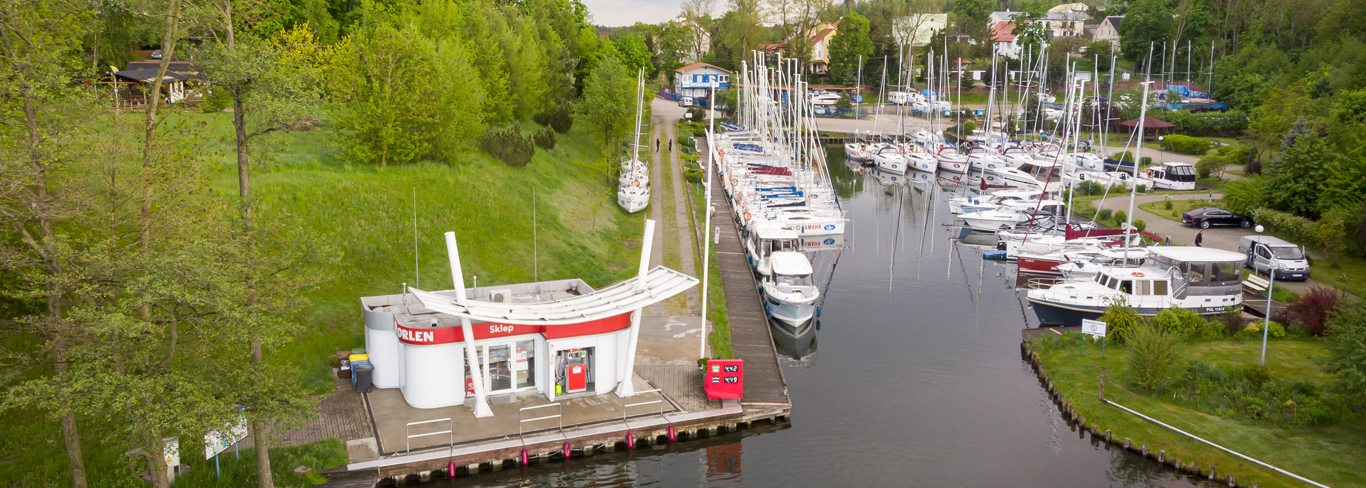
WATER AND WASTEWATER MANAGEMENT
The process of water and wastewater management at the ORLEN Group has for years focused on the optimisation and efficiency of water withdrawal and consumption.
The effectiveness of our responsible management of water resources and investments in state of the art technologies is demonstrated by the developments seen at the Płock refinery over the last 40 years, where steady growth of production and crude oil processing was accompanied by a gradual decrease in the water consumption and wastewater discharge volumes.
Technology in statistics
Water and wastewatermanagement
PKN ORLEN uses 27.7 million cubic metres of water a year, with 900 million cubic metres of water circulating in its systems annually.
Water is essential for the operation of the production plant in Płock. It isused for:
- power generation;
- cooling;
- technical safety.
Water for power generation and cooling purposes is sourced from the Vistula, where as all water for technical safety purposes is produced from wastewater treated on the plant premises, which is an element of a semi-closed loopwater system.
Cooling water is abstracted from the Vistula and thent reated to remove impurities. This water, called processwater, is directed to cooling water towers, where it is added to the water circulating in the closed-loop system between the cooling water towers and the production units. Coolingwater needs to be refilled to make up for its losses (of about 2% of the total amount of the cooled water) caused by partial evaporation during water cooling processes occurring in the cooling towers.
Water for technical safety purposes is water produced from treated wastewater and subjected to a final purification process. Water for fire-fighting purposes is directed to the Company's fire hydrant network to be used in case of fire. A part of this water is directed to the utility water hydrant network and isused for other technical purposes at the plant.
The plant also produces drinking water for its own use from water drawn from the Company’s owned wells located in the area of Biała Stara and treated on the premises of the production plant.
Upgrade of pump units - objectives and results
Efficient water and wastewatermanagement
Approximately 3.5 million cubic metres of wastewater per year is recycled to produce water for fire protection purposes at the plant.
Upgrade of pump units - results
Energy saving measures include:
1. Operation of pumps with frequency inverters.
2. The inverter can control any of the power supply units available at the pumping station. The leading parameter for the operation of an inverter is the pressure in an operating manifold.
3. Pumping water through three manifolds instead of one.
4. Each meter of pumping height means some 10.5 kW of additional power consumption. If a single pipeline is in operation, linear losses grow in line with the increase in flow velocity, resulting in an increase in the pumping height and thus in higher power consumption.
5. Maintaining a low water level in the tower tanks reduces the pumping height and thus mitigates power consumption growth.
6. The purchase of a new inverter improved the control efficiency by a few per cent. Effect: reduction of electricity consumption by 3,000,000 kWh a year.
Comparison of water withdrawal and electricity consumption rate for water withdrawal in 2013–2020
WATERKey Performance Indicators for the ORLEN Group
Withdrawal of water
Sweet surface waters are the main water source for the Group companies; their dry residue is below 1,000 mg/l.In accordance with the applicable permits, these waters were withdrawn by the ORLEN Group’s largest companies: the Energa Group, ANWIL, IKS Solino, PKN ORLEN, ORLEN Południe, ORLEN Lietuva, Unipetrol, Paramo and Spolana, and then distributed through water mains to their own production facilities, to other ORLEN Group companies and to third parties. The volume of surface water, groundwater and mains water withdrawn by the ORLEN Group in 2020 totalled nearly 331.8 million m3, of which the largest amount was withdrawn by EnergaElektrownieOstrołęka (236.7 million m3 of surface water and 202,300 m3 of ground water).
PKN ORLEN withdrew a total of 26.9 million m3 of water in 2020 (including 26.5 million m3 of surface water and 0.4 million m3 of groundwater), which means a decrease of more than 1.3 million m3 (some 5%) on 2019. The water taken up contained less than 1,000 mg / l of dry residue.
Water consumption at ORLEN Group companies
Water intake point |
Water withdrawn [m3] |
||
2020 |
2019 |
Increase/decrease [%] |
|
Surface water |
327,031,321 |
89,090,471 |
267.08 |
Groundwater |
1,581,749 |
1,555,827 |
1.67 |
Mains water |
3,157,075 |
3,441,486 |
-8.26 |
Total |
331,770,145 |
94,087,784 |
252.62 |
The increase in water withdrawal volumes reported at the ORLEN Group is related to the inclusion of Energa Group companies, whose total surface water, ground water and mains water withdrawal volumes amounted to over 246.3 million m3.
In addition, Energa OZE abstracted 18.4 billion m3 of water for the operation of hydroelectric power plant turbines. The entire volume of that water was returned to the environment unchanged. The high-efficiency turbines operated by Energa OZE support greater electricity generation with less water flow; moreover, the water moving through the turbines and through the bleed system is aerated, which is beneficial to aquatic organisms, especially during periods of high temperatures.
Climatic conditions and demand for water are key factors that have a direct impact on the operation of ORLEN Group production plants. The risk of droughts, due to climate change and low levels of rainfall, can cause freshwater deficits in rivers and groundwater layers.
Four plants operated by the ORLEN Group: the power plant in Kalisz and refinery units in Litvinov, Jedlicze and Mažeikiai are located in areas which, according to WWF (https://waterriskfilter.panda.org/en/Explore/Map), have been identified as areas of increased water deficit.
Amount of water withdrawn from areas with impaired water availability in 2020
Water intake point |
Water withdrawn [m3] |
Water resource pressure |
|
Surface water |
Groundwater |
||
Mažeikiai |
1,706,897 |
352,522 |
Low risk |
Jedlicze |
478,980 |
70,202 |
Medium risk |
Litvínov |
15,837,206 |
0 |
Medium risk |
Kalisz |
122,968 |
0 |
High risk |
Total |
18,146,051 |
422,724 |
|
Reuse of recovered water
In recent years, the ORLEN Group has made a number of investments that result in a more efficient use of water and increase the safety of water and sewage systems.
ORLEN Group companies recover water from treated effluents and use steam condensate circulation systems and closed water systems for cooling in production processes.
In 2020, 2.1 billion m3 of water circulated in their cooling systems with a total capacity of 268,930 m3. More than 25 million m3 had to be refilled as a result of losses and evaporation. This means that 2 billion m3 of water remained in constant use. Moreover, the companies recovered over 9 million m3 of steam condensate; after its proper pressure was restored at the companies’ CHP plants, the condensate was returned to the units. Production of utility water from treated effluents is carried out at PKN ORLEN and ORLEN Lietuva. In this way the companies were able to obtain more than 7.4 million m3 of water for fire protection and other purposes.
In total, more than 2 billion m3 of water circulated in Group companies’ units in 2020, accounting for 640% of the water withdrawn, i.e. more than six times more than the water withdrawal volume.
WASTEWATERKey Performance Indicators for the ORLEN Group
Effluents from all ORLEN Group companies are directed to industrial and rainwater sewage systems and then undergo treatment. Wastewater discharged to the environment is metered. In 2020, the ORLEN Group’s overall discharges exceeded 300 million m3, which included more than 298 million m3 of industrial wastewater. A significant volume of wastewater was discharged by Energa Elektrownie Ostrołęka: 235 million m3.
In addition to PKN ORLEN, the following companies operate their own wastewater treatment systems: Energa Elektrownie Ostrołęka, Energa Kogeneracja, ANWIL, Ship-Service, Spolana, Paramo, Unipetrol, ORLEN Lietuva, ORLEN Południe, ORLEN Paliwa, ORLEN Budonaft, Naftoport, IKS Solino, Benzina and ORLEN Baltics Retail. All wastewater undergoes a treatment process which includes mechanical, physical, chemical and/or biological treatments. Once wastewater is treated in accordance with the companies’ integrated permits, it is discharged into rivers: Vistula, Oder, Narew, Elbląg, Elbe, Bílina, Dubulis, Obelaukis, Vltava, Jasiołka, Prosna, Brzeźnica, Ropa and Sowlina, and to the Baltic Sea. The other companies divert their wastewater streams to wastewater systems of other Group companies or third parties.
Treated wastewater at the ORLEN Lietuva refinery and at the production plant in Płockis partly recovered, which reduces the amount of water withdrawn from the environment for utility and fire-fighting purposes. In 2020, ORLEN Lietuva and PKN ORLEN reused 4.1 million m3 and over 3.3 million m3 of wastewater, respectively.
At ANWIL’s PVC plant, heat is recovered from process wastewater.
924,000 m3 of wastewater were treated by external entities, including 651,000 m3 of industrial wastewater.
The ORLEN Group does not use rainwater collected directly or treated wastewater generated by entities from outside the Group.
Volumes of treated effluents discharged into the environment by ORLEN Group companies
Effluent type |
Volume of treated effluents discharged |
||
2020 |
2019 |
Increase/ decrease [%] |
|
Industrial wastewater |
298,448,352 |
44,397,037 |
572.23 |
Other |
5,608,669 |
6,517,502 |
-13.94 |
Total |
304,057,021 |
50,914,539 |
497.19 |
The increase in the wastewater discharge volumes reported at the ORLEN Group is related to the inclusion of Energa Group companies, where the total volume of effluents discharged to the environment amounted to over 254.7 million m3.
Share of substance loads in effluents discharged into the environment
The substance load in effluents discharged into the environment totalled nearly 70,000 Mg, with sulfates and sulfites representing the largest share of the total load. Sulfate and sulfite volumes went down 3% year on year.