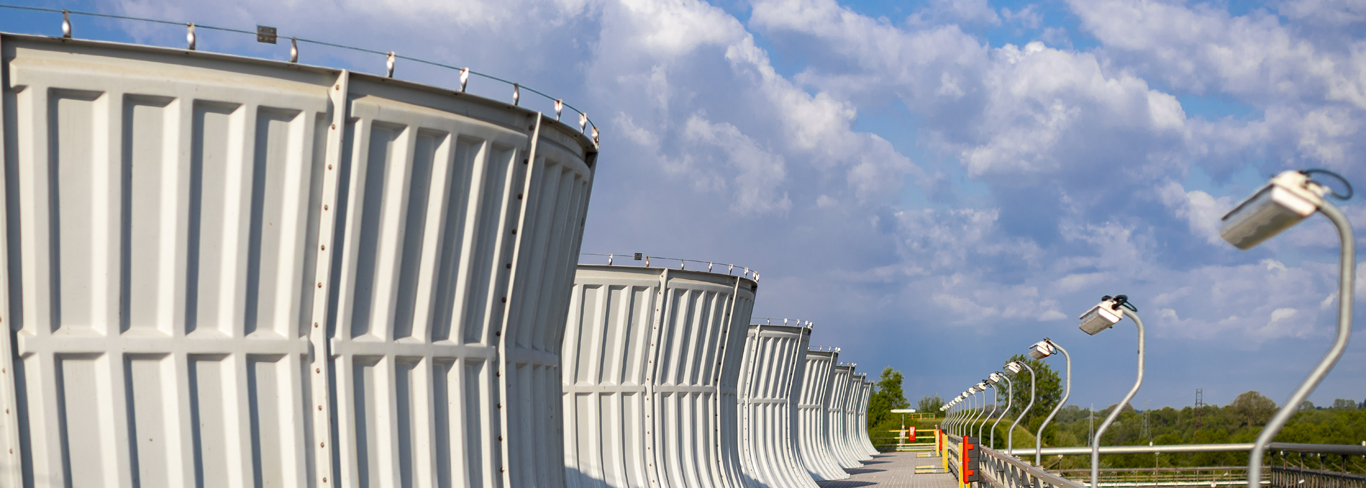
INTEGRATED MANAGEMENT SYSTEM
The ORLEN Group supplies highest-quality products to its customers, while striving to make its operations as neutral to the natural environment as possible, to achieve superior energy efficiency, and to maintain high OHS and information security standards.
To deliver on that promise, the Group has the Integrated Management System (IMS) in place. The IMS comprises :
- Quality Management System based on the PN-EN ISO 9001 and AQAP 2110 standards,
- Environmental Management System based on the PN-EN ISO 14001 standard,
- Occupational Health and Safety Management System based on the PN-EN ISO 45001 standard,
- Energy Management System (SZEn) based on ISO 50001,
- Information Security Management System based on PN-ISO/IEC 27001,
- International Sustainability & Carbon Certification System (ISCC EU),
- Sustainability Certification System for Biomass and Biofuels (KZR INiG),
- Factory Production Control System (ZKP),
- HACCP Food Safety Management System compliant with Codex Alimentarius standard,
- Quality Management System based on the PN EN ISO/IEC 17025 standard (in place at all the organisational units which conduct research or tests using methods that require approval by the Office of Technical Inspection (UDT)),
- Risk Based Inspection Management System (RBI).
The scope and rules governing the operation of the Integrated Management System are specified in:
- Integrated Management System (IMS) Book with schedules,
- Energy Management System Book,
- Factory Production Control (ZKP) Book,
- Risk-Based Inspection (RBI) Book,
- JET A1 Book – supervision of quality of aviation turbine fuel during production, storage and distribution,
- PN-EN ISO/IEC 17025 System Book,
- HACCP Book,
- System procedures approved by the President of the Management Board – Chief Executive Officer/ Members of the Management Board,
- Maps, charts and metrics for the identified processes,
- Operating procedures/manuals approved by Directors/Managers for their respective processes/areas.
In 2020, the following key projects were completed with respect to the Integrated Management System:
- Improvements were made to PKN ORLEN S.A.’s certified Integrated Management System.
- Cooperation with certification bodies with respect to Management Systems surveillance was continued.
- The OHS Management System was adapted and recertified in compliance with ISO 45001.
- Improvements were made to the Energy Management System and the certification based on ISO 50001 requirements was maintained.
- Improvements were made to and the certification was maintained for the Factory Production Control (ZKP) System.
- Tools supporting the oversight of documented information were refined.
- Efforts were continued to obtain another RBI Management System certification.
- The Food Safety Management System was maintained and improved.
- The International Sustainability & Carbon Certification System (ISCC EU) and the Sustainability Certification System for Biomass and Biofuels (KZR INiG) were improved and certified.
- The PKN ORLEN S.A. Food Safety Policy, aimed at ensuring that all activities related to food guarantee its appropriate quality and safety, was developed and issued.
- The IMS Policy was updated to reflect the upgrade of the OHS Management System from PN-N-18001 to PN-ISO 45001 and the issuance of the separate PKN ORLEN S.A. Food Safety Policy.
Detailed information on the results of the activities carried out based on the Integrated Management System in 2020 is available in other parts of this Integrated Report, for example:
-
Description of the capital expenditure on environmental protection and the key environmental impact indicators can be found in the section ‘Environment and climate’.
-
Statistics demonstrating compliance with the highest safety standards are shown in ‘Employees and contractors'.
- Data on the effects of customer health and safety activities is presented in ‘Responsibility towards customers’.
-
The results of energy management are described in ‘Energy management'.
- Data on the use of biocomponents meeting the sustainability criteria is contained in ‘Feedstocks and production processes’ .
Process-basedmanagement
PKN ORLEN applies a process-based approach involving identification and mapping, based on an analysis of the context of the entire organisation’s operations, of the processes which are necessary to ensure compliance of its products and services offered to customers with relevant requirements, while maintaining pro-environmental production methods and pro-environmental approach, and minimising the environmental impacts, continuously improving the safety of working conditions, and meeting requirements in all areas relevant to security of information processed by the Company. The process sequence has been defined, as well as the relationships between the processes, which constitute a multi-layered mechanism that facilitates identifying and satisfying customer expectations. Individual processes are monitored and the achievement of their objectives is evaluated by checking process metrics and comparing them against adopted benchmarks. This approach allows us to manage and improve processes relying on real, measurable data. In line with the risk-based approach, process owners are responsible for identifying threats (risks) and opportunities that can potentially affect the operation and efficiency of the processes – meeting customers’ requirements and taking appropriate and ‘adequate’ measures. A process-based system of internal audits is used, which operates in accordance with a dedicated procedure and checks compliance of individual areas with the adopted standards. The improvement measures we take cover internal and external factors and identify opportunities as they open to the organisation. Any improvements to the Integrated Management System are decided on by the Company’s senior management, in line with the IMS evaluation procedure. The procedures in place specify how particular activities are to be carried out in each area.
A total of 54 processes/sub-processes were identified at the Company, for which 135 metrics were defined. The process charts specify the metrics, which include three-tiered criteria for evaluating effectiveness, defined as acceptable, requiring monitoring, or requiring corrective measures. The assessment of the delivery of the metrics is made on the basis of data entered by the process/sub-process owners into the Dok-system.
The precautionary principle, environmental damage prevention and effective workplace safety and information security management are ensured through standardisation and implementation of systemic mechanisms, which also include preventive measures. The precautionary principle is supported by systemic mechanisms that pre-emptively address potential irregularities and are based on process analysis and elements of risk and opportunity assessment. In accordance with the precautionary principle, business activities involve taking measures to prevent environmental degradation.
Auditsexternal and internal verification of the Integrated Management System
In 2020, PKN ORLEN was subject to a periodic external audit. As a result, the Company obtained certificates of compliance with international standards for its activities.
The Company’s activities are assessed by certified external bodies, which audit the areas covered by the management systems in place on an annual basis. In 2020, these included:
- AQAP 2110 recertification audit by CCJ WAT, held in Płock on June 2nd–5th 2020. Due to COVID 19, the audit was conducted remotely, from the Company’s headquarters in Płock. The audit did not identify any irregularities and new certificates of the Quality Management System compliance with the AQAP 2110 and ISO 9001:2015 standards were obtained.
- ISCC EU recertification audit by Bureau Veritas Polska: stage one – remote audit on May 26th–27th 2020, and stage two – site visitson July 30th and September 23rd 2020; stage two of the audit was held to maintain validity of the certificate issued after the remote part and consisted of a site visit in Płock on July 30th 2020 and at the Fuel Terminal in Ostrów Wielkopolski on September 23rd 2020. Due to COVID 19, the audit was conducted remotely. It did not identify any non-compliance and the system was recertified as compliant with Renewable Energy Directive / ISCC EU Certification System.
- Factory Production Control System audit by Polskie Centrum Badań i Certyfikacji on May 26th–27th 2020. Due to COVID 19, the audit was conducted remotely. The audit did not identify any non-compliance and validity of the certificates was maintained.
- Recertification audit of the Sustainability Certification System for Biomass and Biofuels (KZR INiG) by Bureau Veritas Polska, held on June 25th and December 3rd 2020 (remote audits), as well as on November 20th 2020 in Płock. Due to COVID 19, the audit was conducted remotely. The audit did not identify any non-compliance and a new certificate was obtained for the production of the bio-component: liquid bio-hydrocarbons in the co-hydrogenation process.
- IMS surveillance audit in connection with the upgrade to ISO 45001, conducted by Bureau Veritas Polska in Płock, Olszanica, Żurawica, Widełka, Gutkowo and selected service stations on September 4th–11th 2020. Due to COVID 19, the audit was conducted on a hybrid basis – remotely and through site visits at service stations. The audit confirmed correctness of the system operation. It was followed by a recommendation to issue new certificates confirming the system’s compliance with the requirements of the PN-EN ISO 9001:2015, PN-EN ISO 14001:2015, ISO 45001 and PN-EN ISO/IEC 27001:20014 standards. The audit did not identify any non-compliance.
- ISO 50001 surveillance audit by UDT-CERT, held in Płock and Włocławek on December 3rd–4th 2020. The audit did not identify any non-compliance and validity of the certificate was maintained.
The external audits identified no instances of non-compliance and confirmed correctness of the existing systems operation. Also, recommendations were received for new certifications.
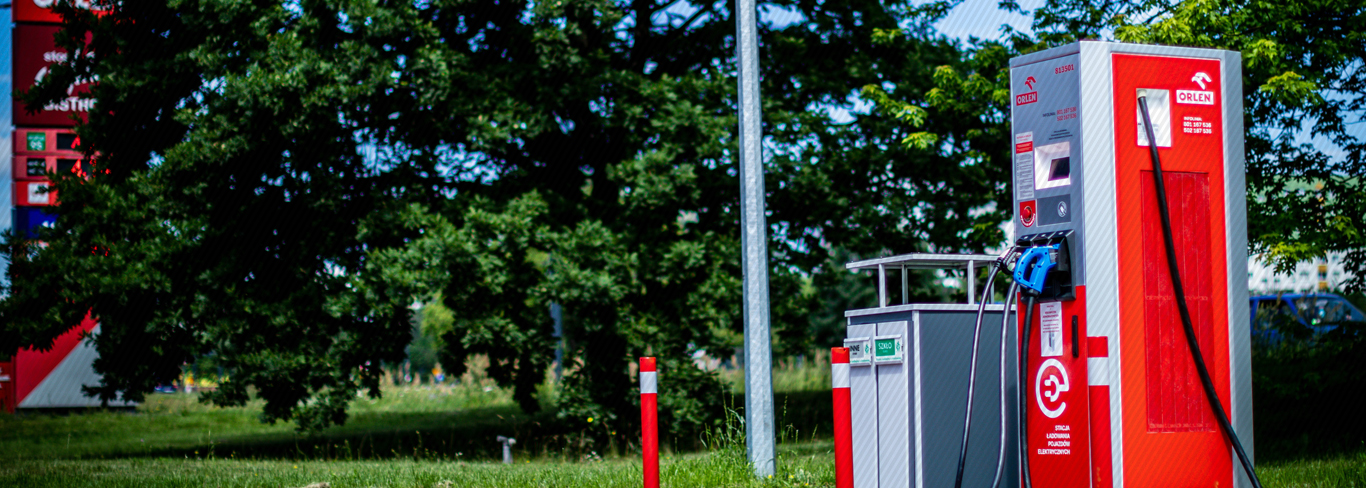
A total of 535 audits were completed in 2020, including: 494 internal IMS audits, 15 audits held to verify whether CO2 emissions are monitored correctly, 6 audits of the Energy Management System, 13 second party audits, and 7 ISCC audits.
Internal auditsystem
The audits confirmed compliance with the requirements of the applicable systems. The auditors also identified the elements that require improvement.
The certified Management Systems in place support:
- The organisation’s ability to meet customer needs and expectations (having a certificate is often a key formal condition for establishing a business relationship; access to domestic and international markets).
- Building the competitive advantage.
- Stronger reputation of the company and its products and services both among existing and prospective customers.
- Better organisation of internal documentation (a process-based approach helps to manage the organisation and eliminate inefficiencies).
- Confidentiality (access to information is limited to authorised personnel).
- Integrity (ensuring accuracy and completeness of information and the methods used).
- Availability (authorised users are given access to information and resources when needed).
- Improved quality (lower number of customer complaints).
- Earnings growth (because of lower internal costs achieved through improved quality that meets customer expectations).
- Enhancing environmental measures and contributing to environmental protection.
- Cost reductions achieved through lower energy consumption and lower waste volumes.
- Reduced risk of crisis (avoiding industrial accidents).
- Ensuring compliance with applicable requirements (avoiding penalties).
- Promoting pro-environmental thinking.
- Identification of threats to employees’ safety and prompt implementation of preventive measures.
- Engaging all employees in creating a safe workplace - cost reductions due to lower accident rates.
- Employees’ trust in the organisation and a sense of responsibility for its activities.
Certificates issued to PKN ORLEN:
IMSdocumentation
Apart from the regulations contained in the System Books, the Integrated Management System currently includes 74 procedures:
- 8 Environmental Management System procedures
- 3 procedures for AQAP 2120 requirements
- 53 Quality Management System procedures
- 2 Occupational Health and Safety Management System procedures
- 5 Information Security Management System procedures
- 1 Sustainability Certification System for Biomass and Biofuels procedure
- 1 Energy Management System procedure
- 1 procedure of the co-hydrogenation process certification system
In 2020, the following were updated:
- JET A1 Book – supervision of quality of aviation turbine fuel during production, storage and distribution
- the Risk Based Inspection (RBI) Management System Book
- the Factory Production Control (ZKP) System Book
- the Energy Management System (EMS) Book
Management System based on ISO/IEC 27001key developments
An update to Order No. 40/2020/DG of July 9th 2020 on protection of classified information was issued, introducing the Classified Information Protection Policy to be applied at PKN ORLEN S.A., in order to lay down the principles for organising the protection and processing of classified information.
In connection with the pandemic, the following information clause was made available: Information clause for a person whose data has been received at covid19@orlen.pl
Efforts were made to continually raise the awareness of threats, particularly ICT and cyber threats, and, recently, also of the coronavirus threat.
Awareness building activities included anti-terrorism and anti-corruption training.
Management System based on ISO 45001key developments
The OHS Management System covers all of the Company’s organisational units. In 2020, PKN ORLEN S.A. took steps related to transition to a new standard. After a positive outcome of an audit carried out on September 2nd-3rd 2020 to verify compliance with OHSAS 18001, we were audited for compliance with the requirements of ISO 45001.
Then, on September 4th–11th 2020, the auditors of Bureau Veritas Polska Sp. z o.o. (BV) conducted a surveillance audit of the Integrated Management System with respect to the Quality Management System, Environmental Management System and Information Security Management System, combined with an upgrade of the Occupational Health and Safety System to ISO 45001.
The audit confirmed that we fulfil the requirements of the new standard and we received certificate No. PL010344/U, issued on November 30th 2020 by Bureau Veritas Certification Holding SAS-UK Branch, which is valid until June 19th 2022.
Management System based on ISO 50001key developments
- Order No. 59/2020/DG of November 25th 2020 on the operation of the Energy Management System at Polski Koncern Naftowy ORLEN S.A. was issued.
- The Energy Management System Book was updated.
- New edition of the Energy Performance Planning and Review Procedure in the Energy Management System PRE/001 was issued.
- Surveillance audit by UDT-CERT: Recommendation to maintain the certified Energy Management System based on the new ISO 50001:2018 standard.
- (Six) fully completed internal audits.
- Energy performance review showing an improvement in the energy efficiency of individual units, with energy intensity reduced by approximately 464,877 GJ and thus annual CO2 emissions cut by 22,820 tonnes. As energy consumption was optimised, production cost savings of PLN 1,391,291 were achieved.
ISCCkey developments
Entities operating in the field of production of bio-components, processing of biomass, purchase, import or intra-Community purchase of biomass or bio-components which are to be counted towards the National Indicative Target (NIT), are obliged to obtain a certificate confirming that they fulfil the sustainability criteria.
At PKN ORLEN S.A., compliance with the sustainability criteria is confirmed by the use of the International Sustainability & Carbon Certification System (ISCC EU), which enables identification of energy carriers produced in a sustainable way using renewables.
ISCC EU is aimed at protecting the biosphere and rational land management, but also sustainable social development and reduction of greenhouse gas emissions, by enabling emission volume tracking at every stage of the biomass and biofuel production process. Implementation of the ISCC is a confirmation that the company cares about environmental protection and builds its image of an environmentally committed business.
ISCC helps producers to organise the biofuels production and distribution processes in accordance with the European legal requirements, and enables potential customers to verify greenhouse gas emissions volumes at each stage of production, i.e. cultivation, harvesting, storage, processing and delivery to the final recipient.
Sustainability Certification System for Biomass and Biofuelskey developments
In 2020, Bureau Veritas Certification Polska granted a certificate to the Company confirming compliance of the production of the bio-component: liquid bio-hydrocarbons in the co-hydrogenation process with the requirements of the Sustainability Certification System for Biomass and Biofuels (KZR INiG), valid for the period from August 19th 2020 to August 18th 2021. The certificate was issued after a remote audit conducted by Bureau Veritas Polska Sp. z o.o. on June 25th 2020.
Bureau Veritas Polska Sp. z o.o. also performed an on-site audit on November 20th 2020 and a remote audit on December 3rd 2020 in order to verify the greenhouse gas (GHG) emissions calculations. We received a positive assessment and are now waiting for its formal confirmation in the form of a report.
The greenhouse gas (GHG) emissions calculations were changed on the basis of data from the production area in 2020 and in consultation with the auditor Bureau Veritas Polska Sp. z o.o.: the requirements for the feedstock to be used in the production of the bio-component (liquid bio-hydrocarbons in the co-hydrogenation process) in the current year were reduced.
HACCP – food safety managementkey developments
1. Update of the HACCP System Documentation, development of new solutions to improve food safety, and preparation of new documents forming part of the HACCP System Documentation in connection with the expansion and calibration of the food and beverage offering and following an analysis of the current documentation by the Food Safety Advisor.
2. Development of the PKN ORLEN S.A. Food Safety Policy, its approval by the President of the Management Board and implementation.
3. Performance of IMS audits, introduction of remote audits due to the pandemic.
4. Completion of audits of the suppliers of food products to the service stations, introduction of remote audits due to the pandemic.
5. Activities improving the skills and qualifications of HACCP auditors, participation in training as part of the process run to calibrate the food and beverage offering.
6. Additional visits and training at pre-trained DOFO stations in connection with the upgrade to the 2.0 standard.
7. HACCP training for newly opened facilities and in the case of new food services offered at CODO stations, as well as for new Stop Cafe/Stop Cafe Bistro/Stop Cafe 2.0 contracts at DOFO stations, introduction of remote training due to the pandemic.
8. Provision of a supervised copy of the HACCP Book to the County Sanitary Inspector in connection with the service station format upgrade to the 2.0 standard.
9. Update of regulations related to food and nutrition security, including regulations introduced for the duration of the COVID-19 pandemic.
10. ‘Chameleon’ project – participation in implementation activities, offering opinions on the solutions and assumptions adopted for the purpose of implementing new retail formats at PKN ORLEN S.A.
11. Development of a procedure necessary for an official approval of the food service activities at PKN ORLEN service stations.
12. Taking steps to expand the HACCP Food Safety Management System documentation by developing: requirements for suppliers of packaging materials for food products, requirements for transport service providers delivering food products to service stations, requirements for food producers, and instructions for sales from food trucks.
13. Operational activities related to the Covid-19 pandemic and requiring review/analysis and development of new documents/instructions and issuing opinions on new documents/instructions, including:
a) participation in teleconferences on coronavirus emergency instructions – discussing and working out preventive measures and human and food safety needs related to the coronavirus outbreak.
b) issuing opinions on the guidelines of the Head of Control and Security Office concerning organisation of the movement of people and materials at PKN ORLEN S.A.’s protected sites due to the potential risk of coronavirus infection.
c) activities undertaken to prepare food handling guidelines for service stations to ensure protection against coronavirus infection; the materials were developed for the needs of Retail and then distributed for use at service stations.
d) preparation of an inquiry to the State Sanitary Inspection on the course of action to take in the case of coronavirus threat or infection.
e) Analysis of and opinions on various issues, including:
- materials relating to planned activities at service stations as regards hygiene and customer service,
- cleaning instructions – cleaning products,
- providing coffee accessories to customers,
- quality and use of disposable gloves,
- quality and use of sanitisers and disinfectants.
Management Systemsat ORLEN Group companies
In 2020, work continued on the ORLEN Group Management Systems with a view to harmonising the management model with PKN ORLEN’s growth strategy. In the reporting period, the Group companies’ activities in relation to Integrated Management Systems were in line with the concept for the optimisation of the IMS functioning. The IMS policies were put in place at the following key companies of the ORLEN Group: PKN ORLEN S.A., ORLEN Administracja Sp. z o.o., Anwil S.A., Basell ORLEN Polyolefins Sp. z o.o., ORLEN Laboratorium S.A., ORLEN EKO Sp. z o.o., ORLEN Asfalt Sp. z o.o., ORLEN Serwis S.A., ORLEN Upstream Sp. z o.o., IKS Solino S.A., ORLEN KolTrans Sp. z o.o., ORLEN OIL Sp. z o.o., ORLEN Administracja Sp. z o.o., ORLEN Aviation Sp. z o.o., ORLEN Paliwa Sp. z o.o., ORLEN Projekt S.A., ORLEN Budonaft Sp. z o.o., ORLEN Lietuva, the UNIPETROL Group, ORLEN Centrum Usług Korporacyjnych Sp. z o.o., ORLEN Południe S.A., ORLEN Centrum Serwisowe Sp. z o.o., and ORLEN Ochrona Sp. z o.o.
The Integrated Management Systems were built based on the following standards:
- Quality Management Systems compliant with ISO 9001:2015,
- Environmental Management Systems compliant with ISO 14001:2015,
- OHS Management Systems compliant with ISO 45001:2015 and PN-N 18001 / OHSAS 18001,
- Information Security Managements System based on ISO/IEC 27001:201-06.
Depending on business needs, the companies maintain the certificates for the systems indicated above.
In addition, depending on the business profiles, legal requirements, customer expectations, etc., some companies obtained certification for the following systems implemented in their organisations: AQAP 2110 Management System, Factory Production Control, Rail Transport Safety Management System (SMS), Rail Transport Maintenance Management System (MMS), Quality Management System for Welding Processes, HACCP Food Safety Management System, ISO 50001 Energy Management System, ISCC EU System, KZR INiG System, ISO 17025 Laboratory Quality Management System.
2020 was a special time because of the pandemic, which forced a number of changes and new activities. The companies successfully modified the rules they apply for surveillance of their Management Systems by using the available IT technologies to a greater extent than before. This included, in particular, participation in online training sessions and seminars, as well as transition to remote audits, both internal and external. Moreover, meetings and consultations with representatives of PKN ORLEN S.A., including those concerning benchmarks, were conducted remotely using the available corporate ICT tools.