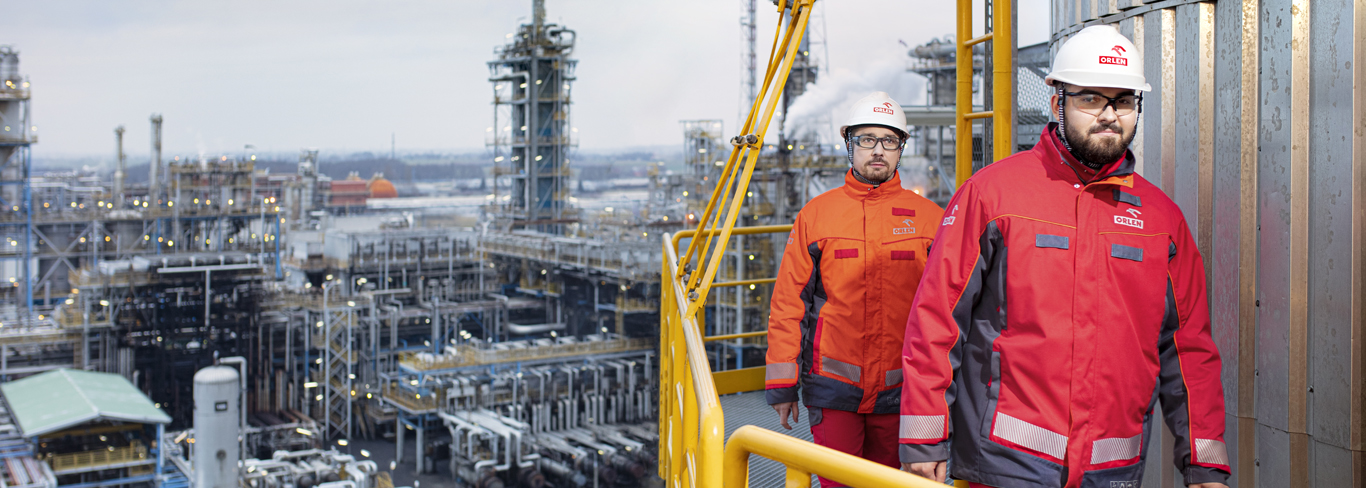
SAFETY OF EMPLOYEES AND CONTRACTORS
Care for the health and personal safety of employees and other stakeholders is a natural and integral part of our organisational culture and business.
In practice, this means that the Group does every thing it can to prevent accidents, industrial failures, fires and other unwanted incidents. This approach to safety management at the ORLEN Group follows from our business philosophy: “People are our most valuabl easset and must be provided with safe working conditions.” Effective management of the occupational, process and firesafety system is a precondition for the ORLEN Group’s growth across all areas of its operations. Therefore, the objective of the area is to address the challenges arising from technological progress in ensuring the stabilisation of operational processes by maintaining their highest safety standards. Our priority goal is to maintain leadership in safety.
SafetyStrategy
The personal, process and fire safety objectives and tasks are defined in the ORLEN Group’s Personal and Process Safety Strategy, covering the following key areas:
- management and leadership – building a workplace safety culture within the Group in line with its values; a combination of individual and group values, attitudes, perceptions, competences and behaviours;
- personal safety – building a safe and healthy working environment for the Group’s employees, including a contractor supervision system; taking preventive measures designed to ensure fire safety at the Group, and setting standards and relevant organisational projects;
- process safety – activities involving definition of methods and measures to protect people and the environment against the consequences of failures and industrial accidents, determination of existing needs before technological, process or organisational changes, organisational and technical measures undertaken at every stage of a process to guarantee safe process management, safety of the process personnel, and thus process reliability.
Structure of the ORLEN Group’s safety management system
Politics and internalorganizational acts
Occupational safety at the ORLEN Group is governed by national legislation applicable to a given area, European Union regulations, harmonised national standards and principles resulting from best practices identified in the fuel and energy industry.
In the area of personal, process and fire safety, uniform Safety Standards, Technical Standards and Guidelines are in place, dedicated to ORLEN Group companies. They contain best practices identified within the companies, as well as standards applied in the areas under consideration by industry leaders. In 2020, the implementation of a uniform safety framework was continued at the ORLEN Group as part of the ‘Safety Plus’ project, comprising 15 standards representing the highest safety benchmarks in the fuel and energy industry. The project will be completed in 2021.
In addition, the companies have systems of internal by-laws in place that include personal, process and fire safety policies, rules, internal orders, procedures, manuals, work instructions etc.
A significant majority of ORLEN Group companies have an Occupational Health and Safety Management System conforming to PN-N-18001 / OHSAS 18001 / ISO 45001 in place – certification covers their businesses and only a single process exemption has been applied. The certification extends to all employees of the organisations which have this system in place.
The ORLEN Group’s production companies have implemented a Process Safety Management System conforming to the US OSHA 1910.119 standard, as well as to Guidance of meeting expectations of The Energy Institute Process Safety Management Framework. The System provides an effective framework for achieving operational excellence, as it improves technical safety of the process, storage and auxiliary units, and thus prevents any undesirable events that could affect the safety of staff and/or production processes. The Process Safety Management System, as a component of PKN ORLEN’s overall management and organisational system, was introduced to ensure the highest safety standards in the workplace and meet the national requirements of Art. 252 of the Environmental Protection Law of April 27th 2001 (consolidated text: Dz.U. of 2017, item 519, as amended) with respect to systemic process safety management and further improvement of the effectiveness and efficiency of measures aimed at preventing major industrial accidents.
Furthermore, the following regulations are in place within the ORLEN Group that have been implemented by PKN ORLEN in the first place:
ORLEN Group’s OHS Strategy until 2021 – a new OHS management concept, based on building and developing uniform safety standards for the ORLEN Group while enhancing operational excellence and excellence in preventive measures related to personal and process safety. The strategy covers the following strategic areas: management and leadership, personal safety and process safety.
Comprehensive Prevention System – the principal element of the OHS Management System, which consists of internal organisational documents related to occupational health and safety, fire and chemical safety, radiation, technical and process safety. These include: Process Safety Management System at PKN ORLEN, Radiation Safety Instruction at the Płock production plant and Włocławek PTA plant, Fire Safety Rules of PKN ORLEN, and Comprehensive Chemical Rescue Plan.
PKN ORLEN Safety Points are a set of basic principles required to be observed together with all applicable regulations and standards. Safety Points for PKN ORLEN Company-owned Service Stations are the key rules that must be adhered to on the premises of the service stations owned by PKN ORLEN.
The Safety Points represent requirements describing the attitudes and behavioursexpected by the ORLEN Group companies of their employees and contractors in and outside their day-to-day work. Thoserequirements, together with all applicable laws, instructions and standards, must be complied with by all employees and contractors (regardless of their position), as well as by guests. Individuals who fail to follow the prescribed rules are at risk of being subject to disciplinary action if such non-compliance is revealed.
Third Party ContractorSafety Management
A model for a third party contractor management system has been developed and implemented with a view to meeting the following aspirational objectives: ZERO ACCIDENTS, ZERO FIRES, ZERO TOLERANCE FOR UNACCEPTABLE RISK.
The following goals were continued in 2020:
- ensuring that the assignments for contractors are professionally prepared,
- existence of clear rules,
- raising awareness of the Company’s employees, third party contractors and their employees,
- ensuring that work is carried out safely and correctly,
- confirming completion of training for some specific locations,
- communicating of and fast response to threats.
As part of the Third Party Contractor Safety Management process:
- relevant objectives have been written into the ORLEN Group Personal and Process Safety Strategy 2017–2021, including to improve the contractor management system and gain contractors’ commitment to the shared vision of working together to create a safe workplace,
- contractor accident rates are monitored using safety KPIs – detailed analysis of contractor workplace accidents and TRR,
- M2 Subcontractor Management standard has been implemented under the Safety Plus project,
- the ORLEN Group has in place a safety standard entitled ‘Classification and supervision of safety of third-party companies located on the premises of ORLEN Group companies or providing services to ORLEN Group companies’,
- a system of inspections and audits has been put in place to ensure that contractors are prepared to perform their work and that the work is completed safely,
- Safety Meeting, Lessons Learned, Safety Alerts and other projects are run at the ORLEN Group, and PKN ORLEN operates the Training Centre.
Also, the Process and Fire Safety Reports and other documents are issued to ORLEN Group representatives, providing detailed analysis of contractor workplace accidents and corrective measures taken.
A section dedicated to contractors has been created for PKN ORLEN on the corporate website at www.orlen.pl, headed PKN ORLEN external contractors. It contains up-to-date information concerning safety issues, applicable requirements, training and incentive programmes, and awareness campaigns (‘Report a Hazard’).
Key projects in the areaoccupational health and safety
In addition, in 2020, a Dangerous Goods Transport Team was established at PKN ORLEN. The activities carried out by the team are aimed at ensuring compliance with the provisions of the ADR Agreement (concerning the international carriage of dangerous goods by road) and the RID Regulations constituting Annex C to the Convention on International Carriage by Rail (COTIF) (concerning the international carriage of dangerous goods by rail) of the storage processes implemented in the company, storage, handling and transportation of dangerous goods. The team verifies the correctness of the preparation of the transport documentation, checks the driver's qualifications and compliance with the regulations of the vehicle that has been ordered to transport dangerous goods. The completeness and correctness of the equipment that should be in the vehicle is checked. The team supervises the proper storage and labeling of hazardous waste generated at the installations of the Production Plant in Płock, PTA and CCGT Plants in Włocławek, as well as at the Railway Terminal in Płock and Fuel Terminals. The regulations in force at PKN ORLEN concerning trade in dangerous goods are also verified and updated. The team prepares an annual report on the transport of dangerous goods, which, in accordance with the regulations, is submitted to the Provincial Road Transport Inspector (WITD). The tasks of the team also include the organization and training of employees in the field of safety of operations related to dangerous goods. For the needs of organizational units of PKN ORLEN, an e-mail address was sent to which questions concerning the handling of hazardous materials in the ORLEN Group are sent.
Continuous improvement of the occupational safety management system
The ORLEN Group engages in various efforts to continuously improve its occupational safety management area. These include but are not limited to: setting and pursuing strategic objectives at the ORLEN Group and company level, monitoring occupational safety KPIs for the companies and the Group, developing OHS improvement plans, annual analysis of the OHS situation, taking measures to improve the employees’ and contractors’ work safety culture (such as: ‘Safe Maintenance’, ‘Safe Contractor’, ‘Safe ANWIL’, ‘Report a Hazard’, Behaviour-Based Safety programme, ‘Safety and Health Protection Days at the ORLEN Group’ etc.), operation of external and internal control and audit systems, an extensive employee and contractor training system, incentive schemes for employees and contractors (such as the ‘OHS Incentives Programme’, the ‘Safety Eagles’, ‘Best Practices in Personal and Process Safety of the ORLEN Group 2020’ and ‘Millions of Accident-Free Man-Hours of ORLEN Group Employees and Contractors’ competitions), implementation of post-audit recommendations, preventive and corrective measures identified in the occupational safety area, implementation of best practices identified in the fuel and energy industry.
Consultations withexternal advisors and cooperation with universities are carried out with a view to improving the safety management system. In 2020, some companies carried out consultations and provided training on the ISO 45001:2018 Occupational Health and Safety Management System, while PKN ORLEN continued its strategy of cooperating with universities.
ORLEN Group companies pursue occupational safety objectives and perform occupational safety functions with the use of their in-house OHS services supported by ORLEN Eko’s resources, or with limited outsourcing of OHS services by companies with a small workforce.
Best practices are identified on an ongoing basis through experience sharing across the ORLEN Group and drawing on the lessons learned by other oil and gas companies with global footprint. The projects being implemented include the LOTO System and the Employee Support System.
Control and audit system
Internal audits of the companies are held regularly at the ORLEN Group. In 2020, one consultancy visit (audit) and four re-audits were carried out. Due to restrictions on international travel applicable in the Czech Republic and Lithuania, some of the scheduled consultancy visits to foreign Group companies were cancelled. Visits to the other companies took place as scheduled, observing all sanitary practices.
The audits include an important component called ‘Safety Walks’, consisting in safety reviews at the visited facilities. Results of the assessments and observations made during such visits serve as the basis for formulating and implementing correction and refinement plans and workplace health and safety improvement plans. Audits carried out at the Group companies include internal audits, audits by certification bodies, and audits by risk management consultancies. In accordance with an approved methodology, regular safety audits are conducted at the contractors performing work for the ORLEN Group.
Cooperation between PKN ORLEN and universities
PKN ORLEN established cooperation with the Main School of Fire Service in Warsaw. The parties to the agreement declared cooperation consisting in initiating and running joint teaching, research and development projects, expert support and technical consulting in the area of fire, chemical and process safety, as well as some aspects of occupational health and safety.
Cooperation was continued with the Łódź University of Technology (via the Education Centre in Płock) in a postgraduate programme on industrial process safety.
Moreover, the fourth edition of Technical Safety lectures was delivered in 2020 as part of full-time and extramural curricula of the Chemical Technology studies. It was a continuation of the project carried out in 2017–2019 by the Occupational Health and Safety Office and Technology Office, and by the Warsaw University of Technology Branch in Płock. The initiative involved a series of expert lectures, conducted in accordance with PKN ORLEN’s concept for educating its future engineering staff in areas relevant to the oil processing and energy industries.
The Employee Support System is a behavioural programme aimed at encouraging safe and eliminating unsafe behaviours. Its implementation is one of the multi-directional measures to improve the Company’s safety culture.
The Lockout - Tagout (LOTO) system is a scheduled activity which consists in cutting off power supply to industrial equipment and machinery whenever maintenance or repair work is performed.Lockout prevents employees from switching on the machine until it is disabled. Tagout refers to a tag which informs and warns that a given machine is locked out while maintenance work is being performed, and may not be switched on until the tag is taken off. The system has been implemented to eliminate accidental and uncontrolled switching on of machines or hazardous energy releases during operation, development, repair and maintenance works, and thus prevent accidents and incidents resulting from inadvertent start-up or re-energising of machines, devices or installations.
The ORLEN roup runs the ‘Best Practice in Personal and Process Safety of the ORLEN Group 2020’ competition (former ‘Good OHS Practice’ competition), dedicated to ORLEN Group companies. The aim is to spread good practices in safety that promote a pragmatic and modern approach to that area, including any technical, qualitative, efficiency enhancing, communication, organisational and infrastructural solutions, thus helping to improve and streamline the components of OHS management as well as to boost employee motivation. The competition provides an opportunity to share knowledge and experience in fostering a safety culture between different ORLEN Group companies. There is also another competition dedicated to the ORLEN Group companies, called ‘Millions of Accident-Free Man-Hours of ORLEN Group Employees and Contractors’. The aim of the competition is to promote accident-free work. In 2020, we held the 8th edition of the ‘Best Practice in Personal and Process Safety’ and the 6th edition of the ‘Millions of Accident-Free Man-Hours of ORLEN Group Employees and Contractors’.
In 2020, work was carried out to maintain the Process Safety Management System based on OSHA 1910.119. It provides a more effective framework for achieving operational excellence, as it guarantees technical safety of the process, storage and auxiliary units, and thus prevents undesirable events that could affect the safety of staff or processes.
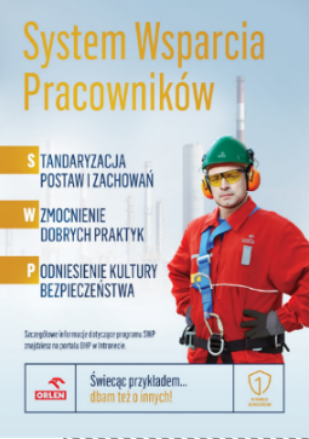
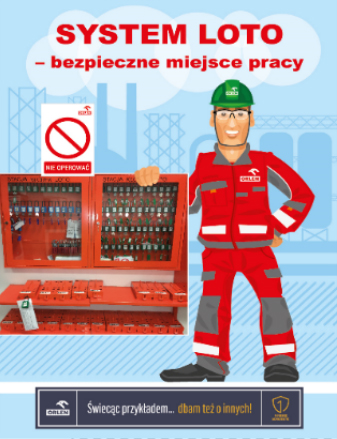
As part of maintenance and improvement of the Process Safety Management System, the following Deming cycle activities are required:
- verification of status quo;
- checking the existing regulations / internal policies for completeness and implementing new regulations / policies;
- confirming that each system component has been fully implemented;
- satisfying the system requirements based on regulations / policies and making the necessary improvements.
The verification covers the company’s compliance with the requirements for 14 components of the Process Safety Management System under existing regulations by which a given component has been implemented.
- safety culture – fostering safe behaviours and safety leadership at the Company through management’s decisions and activities aimed at ensuring the highest possible safety standards for the employees and processes.
- safety leadership − invariably the key aspect of building a safety management system and a safety culture − strong, forward-looking leadership and the prominent role of qualified teams and management personnel influencing attitudes and everyday operating activities.
- roles and responsibilities − defining emergency roles and responsibilities at all levels of the organisation and taking measures to build awareness of the need for continuous improvement and prevention, through developing training programmes and providing training to employees responsible for proactive and preventive activities, as well as emergency response training at all levels of the organisation and to other employees on site, including subcontractors.
- information – ensuring availability of information on process safety as the knowledge needed to identify and implement activities facilitating achievement of the organisation’s objectives; this information must be up to date and easily available in the decision making processes.
- mechanisms − deployment of mechanisms facilitating a systematic analysis of the risk of major accident and probability of its occurrence, and therefore enabling its avoidance.
- designing – at any stage of an industrial unit’s life, designing must be based on the applicable standards and guidelines, and should take into account the possibilities and ways of reducing the likelihood of an emergency.
- instructions and procedures − defining instructions for safe operation of process units that use hazardous substances during normal operation, maintenance, shutdowns, and industrial process adjustments.
- supervision over mechanical integrity – continuous monitoring of the technical condition of plant and equipment, performed through periodic inspections, reviews and tests, in accordance with the regulatory requirements and industry standards.
- safe work practices – performing work at a unit in conformity with the highest standards and requirements in order to ensure safety at the work stations and continuity of technological processes, and to prevent emergencies.
- change and project management – using a systemic approach when changes to an industrial process are necessary, in order to identify whether and how the planned changes may impact process safety.
- contractor management – making and abiding by arrangements concerning safe performance of work on the PKN ORLEN premises by contractors’ employees so as to ensure the highest possible safety standards at all stages of such work.
- responding to failures – implementing the requirement to monitor, in accordance with best available practices, the operation of process units using hazardous substances so that corrective measures can be implemented should any deviation from normal operation occur, including due to normal wear and tear or corrosion.
- analysis − assessing the emergency events that have occurred on a regular basis and applying the knowledge gained from incidents at the ORLEN Group or other plants globally, including putting in place mechanisms that foster learning from past experience (lessons learned).
- auditing and compliance assessment – analysing and reviewing regularly the process safety system in terms of its compliance with the relevant requirements; reviewing the Accident Prevention Programme, being one of the key documents and a systematic programme for the implementation of the overriding goal of proactive accident prevention, and the safety management system in terms of their validity and effectiveness, including information on how the validity and effectiveness is documented and approved, as well as the internal operating emergency response plans that are mandatory for upper-tier and lower-tier establishments (i.e. establishments posing a high or increased risk of a major accident).
Hazard identification, risk assessment, analysis of accidents at work
The ORLEN Group companies carry out ongoing hazard identification, risk assessment and analysis of accidents at work. The process includes: developing and updating the Occupational Risk Assessment for individual positions, carrying out work environment studies, identifying hazards in work instructions, and monitoring of working conditions. The ‘Report a Safety Hazard’ programmes run by the companies are an important part of the process. The process is supported by a system of inspections, audits, job reviews and Safety Walks. Group companies have procedures in place that allow employees and contractors to abandon their work if they identify a potential hazard to their health and life. Conclusions formulated in the process of hazard identification, risk assessment and analysis of accidents at work are used as inputs for the continuous improvement of ORLEN Group’s occupational safety system.
‘Report a Safety Hazard’ at PKN ORLEN – the OHS Incentives Programme
The OHS Incentives Programme is an incentive scheme for the Company’s employees. It includes the ‘Report a Safety Hazard’ competition as a component, where employees or their line managers report safety hazards and propose remedial actions via an electronic system. Best entries are rewarded.
There are structured systems in place at ORLEN Group companies to eliminate any reported and identified hazards, and the respective conclusions inform the Plans for Improvement of Occupational Health and Safety Conditions and other documents. The implementation of preventive and corrective measures is verified based on the existing inspection, audit, job review and Safety Walks systems.
For contractors, this process is executed using, inter alia, an existing system of written permits and training (including hazard training) dedicated to third party employees, or development of Safe Working Manuals by contractors. Some ORLEN Group companies have also launched a ‘Report a Safety Hazard to Contractors’ system.
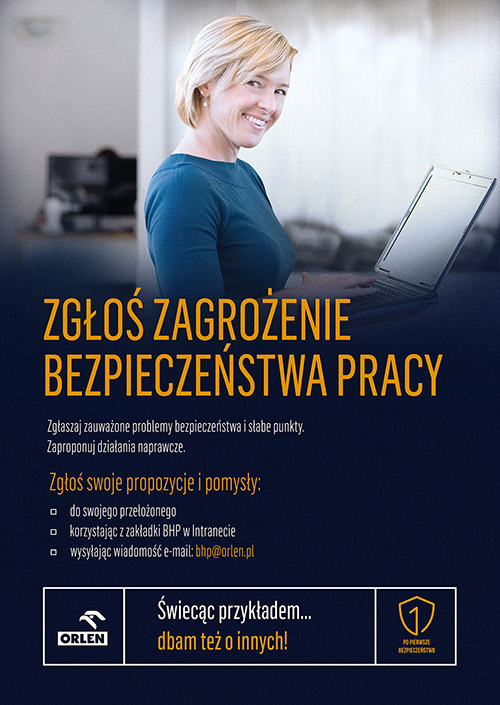
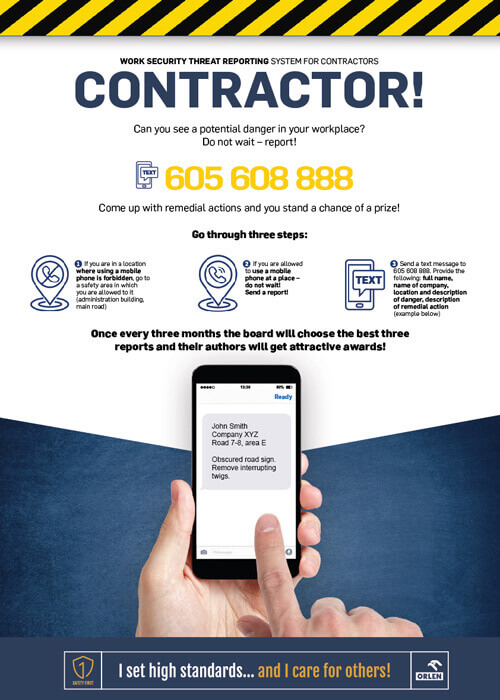
‘Report a Safety Hazard to Contractors’ at PKN ORLEN
The system is dedicated to third party employees. Anyone who identifies an occupational safety hazard may report it by sending a text message to a designated telephone number.
Event tree analysis of accidents at work
A uniform methodology for analysing accidents at work at ORLEN Group companies. It is a chart representing a set of information about the incident, its causes and effects and decisions taken in view of the conclusions reached.
The analysis of accidents at work using the ‘event tree’ method:
Safety Meeting
A continually improved element which requires wider developmentacross the ORLEN Group are interdisciplinary Safety Meetings of representatives of the personal, process and fire safety functions, the Technology Office, and other areas of the organisation. They are held to analyse emergency incidents that occurred at the ORLEN Group by identifying their causes and collecting information about their consequences. On the basis of collected information and available source materials, such as Reports from Emergency/Technical and Reliability Teams (investigation reports), various measures are formulated, which are then addressed to relevant areas of the ORLEN Group companies. The purpose is to learn the lessons and minimise the risk of similar incidents occurring in the future. All information analysed during Safety Meetings is stored within an internal database of PKN ORLEN.
Occupational health services at the ORLEN Group
Employees of the ORLEN Group companies are provided with access to basic medical care. It includes occupational health services, for instance employer-funded preventive care examinations during working hours. The services include issuance of medical opinions and assessment of employees’ capacity to work, monitoring the health of employees in risk groups, examinations for diagnostics of occupational diseases and other work-related illnesses. An occupational medicine doctor is involved in the process of identifying workplace hazards in particular positions as part of an Occupational Risk Assessment, which is developed and then updated as necessary, attends OHS Committee meetings, and is consulted on the contents of first aid kits. In some cases, the scope of services is extended to include additional benefits, e.g. occupational psychology advice. Work environment tests are carried out for particular work posts. In addition, the companies run additional health prevention campaigns and initiatives, such as preventive vaccinations, preventive medical examination packages under the ‘Safe ANWIL for Health’ programme (e.g. TSH tests, abdominal USG examinations, doppler ultrasound examinations of leg arteries), the ‘Energa(y) for Health’ programme, early disease detection programmes (e.g. for coronary and peripheral vessel diseases), densitometric tests, hearing tests, bone tests, mammography imaging, USG examinations for employees’ children, research programme on working environment’s impact on health, and corrective spectacles for employees.
In addition, ORLEN Group employees and their families are offered additional healthcare packages.
Employees’ participation, consultation and communication on occupational health and safety
OHS Committees are in place at ORLEN Group companies (PKN ORLEN, ORLEN Laboratorium, BasellOrlenPolyolefins, ANWIL, ORLEN OIL, ORLEN Południe, ORLEN Serwis, ORLEN Ochrona, IKS Solino, ORLEN KolTrans, ORLEN Eko, ORLEN Centrum UsługKorporacyjnych, ORLEN Centrum Serwisowe, ORLEN Administracja, Energa Group companies in which establishment of an OHS Committee is required.) There is an equal representation of the employer, including a doctor responsible for preventive health care, and trade unions, including Company Social Labour Inspector, on each OHS Committee.
Responsibilities of an OHS Committee include:
- issuing opinions on proposed changes in workplace organisation and equipment;
- analysing conclusions from occupational risk assessments;
- issuing opinions on standards for employee personal protective equipment, clothing and footwear;
- reviewing periodic assessments of health and safety at work;
- issuing opinions on measures to prevent accidents at work and occupational diseases;
- preparing conclusions and issuing opinions on the Plan for Improvement of Occupational Health and Safety Conditions, and assessing its implementation.
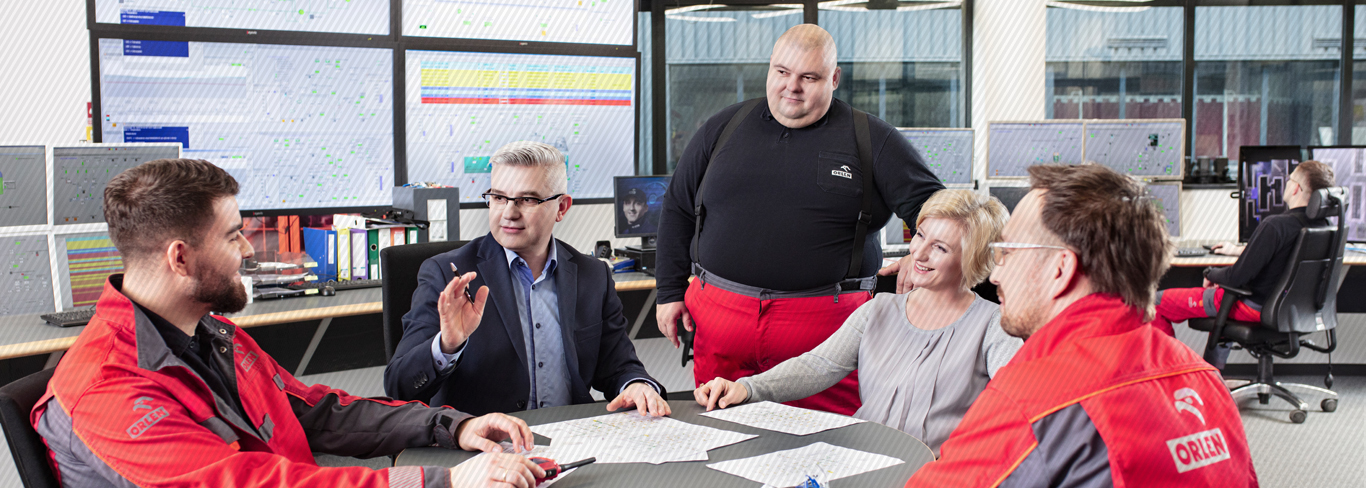
OHS Committee proceedings are held regularly, at least once a quarter. In addition, committees with a similar scope of responsibilities operate at the ORLEN Unipetrol companies, ORLEN Lietuva and ORLEN Baltics Retail.
As regards consultations on occupational health and safety issues at ORLEN Group companies, employees are represented by employee representatives and trade unions. Employee representatives and trade unions are a party in consultations on occupational safety matters, such as development and updates of the Occupational Risk Assessment, employee entitlements to protective clothing and prophylactic meals and beverages, determination of the scope of basic medical care for employees, and iddentification of solutions to improve occupational safety. They are also involved in the activities of OHS Committees.
The ORLEN Group provides access to information on occupational safety through the Company's internal communication system, including the PKN ORLEN intranet available to employees of the ORLEN Group companies. This information is also disseminated during Occupational Safety Days and Topics of the Month as well as security alerts and employee-dedicated programmes such as the Employee Support System.
Employees are involved in the development and improvement of work safety through the ‘Report a Safety Hazard’ system.
PKN ORLEN and ORLEN Unipetrol RPA operate Training Centres.
PKN ORLEN Training Centre
Training Centre is a concept of training employees of external contractors involved in any work at the Company’s production facilities, as well as the Company’s own new hires staffing the production area. It involves detailed checking of the staff’s theoretical and practical knowledge within four thematic blocks: OHS, machinery, electrical systems, and local hazards at PKN ORLEN’s production facilities. Knowledge of and skills in mechanical and electric engineering are checked through practical tasks. A similar initiative addressed to employees has been implemented at ORLEN Unipetrol RPA.
Selected ORLEN Group companies have systems in place to assess the quality of training provided by Training Centres through training assessment or service provider assessment procedures.
Promotionof worker health
Occupational Safety and Health Protection Days at the ORLEN Group
Occupational Safety and Health Protection Days is an annual event dedicated to promoting work safety and healthy lifestyles among the Group’s employees and contractors, and among customers of the PKN ORLEN service stations.Each edition of the project and its planned events present a unique opportunity for employees of the ORLEN Group companies, as well as for external contractors, to participate in activities designed to improve and check their OHS knowledge.
Occupational Safety and Health Protection Days are announced annually by the Head of the PKN ORLEN Occupational Health and Safety Office for all ORLEN Group companies at the same time, although each company prepares its own programme of the event, in keeping with the announced main theme. Participants of the successive editions of Occupational Safety and Health Protection Days at the ORLEN Group have had an opportunity to visit the ‘Driver Awareness’ site, medical booths, VR simulators, gaming areas and OHS competitions, as well as exhibitions of OHS businesses and representatives of the ORLEN Group companies.
In 2020, the format of the event was adapted to the new reality of the COVID-19 pandemic. In order to ensure full safety for our employees, all activities went online, where the participants could checkand improve their OHS knowledge by participating in webinars, educational videos and online lectures. Our employees could learn how to deal with back pain on their own, keep fit while working remotely, cope with negative emotions, and boost immunity during the pandemic. Nutrition-related advice of a clinical dietitian was presented to production staff in the form of videos. In a shortand accessible manner, the expert talked about the rules of proper nutrition when the body needs to function in a shift work system, healthy food, and diseases caused by unhealthy diets.
Prevention and mitigation of occupational health and safety impacts directly liked by business relationships
The Company has in place a safety standard entitled ‘Classification and supervision of safety of third-party companies located on the premises of ORLEN Group companies or providing services to ORLEN Group companies’. Implementation of the standard consists in periodic audits of external companies, which are classified in three categories:
- companies of strategic importance, which have a significant direct impact on the company's functioning, core business, and critical infrastructure – Group A;
- companies providing contractor and execution services, such as day-to-day plant maintenance, and executing smaller investment projects, which have a direct impact on the functioning of PKN ORLEN and ORLEN Group companies located on premises owned by PKN ORLEN, which are not of strategic importance, companies performing particularly hazardous work on premises owned by PKN ORLEN and/or are involved in the collection, storage and transport of dangerous substances produced by the company – Group B,
- companies operating ancillary or support processes, which do not have a direct impact on the functioning of the company, have indirect roles in the operation of processes, act as subcontractors to external companies of strategic importance or carrying out plant maintenance activities, which do not work on operating production facilities – Group C.
External companies classified in:
- Group A are audited at least once a year;
- Group B are audited using the sampling method at least once every three years;
- Group C are not audited, but may be audited at the request of the Head of the PKN ORLEN Occupational Health and Safety Office.
The process includes a comprehensive audit covering, among other things: the company's certified safety management systems, risk and hazard management, accident and crisis identification systems, hazard reporting and mitigation programmes, work safety culture building and improvement area, management of employee conduct, work organisation, fire, process and technical safety.
In addition, the ORLEN Group companies regularly assess suppliers in terms of safety of their work.
Other projectsin the field of occupational safety
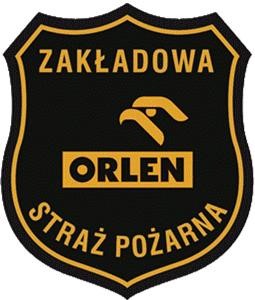
The core responsibility of the Company Fire Brigade is to carry out rescue and fire-fighting activities on the premises of PKN ORLEN, as well as in the entire territory of Poland as part of the National Rescue and Firefighting System and the Assistance System for the Transport of Hazardous Materials (SPOT), and to supervise the readiness of the Company’s facilities for rescue and fire-fighting activities.
Furthermore, the Company Fire Brigade provides chemical and technical rescue, seals leaks, man’s safety stations under plant emergency conditions and during hot works on the premises of the production plant in Płock, and performs fire prevention functions. Firefighters specialise in firefighting in the refining and petrochemical industry, chemical rescue activities, as well as water rescue, technical rescue, medical care at first responder level and rope rescue activities. For several years, they have been actively cooperating with fire brigades operating across the ORLEN Group by taking operational and preventive measures for safety improvement. Firefighters are equipped with more than 20 specialist firefighting and rescue vehicles, high volume pumps and water cannons, a rescue boat and specialist protective equipment for staff. In 2020, measures were undertaken to improve and develop fire safety at the ORLEN Group. Members of the PKN ORLEN Fire Brigade participated in dedicated courses and training, covering prevention, rope rescue, water rescue operations and rescue diving, as well as operation of unmanned aircraft (drones).
Emergency drills involving employees and rescue and firefighting services
Regular emergency drills are conducted at the ORLEN Group companies, building employees’ knowledge of how to behave in an emergency. The drills are also an opportunity to improve cooperation with national rescue services a view to minimising the potential consequences of an industrial accident.
Development of the Fire Safety function at the ORLEN Group
Since March 1st 2020, Company FireBrigades of the ORLEN Group have operated under the segment-based management system. These are nine fire brigades, located in Płock, Włocławek, Trzebinia, Jedlicze, Mažeikiai, Litvinov, Neratovice, Pardubice and Kolín. The process to implement the segment-based management system included a number of measures initiated and implemented to ensure internal standardisation of the fire protection area.
Production assets integrity monitoring and plant maintenance programme
Timely inspection and supervision activities are key to maintaining the integrity of fixed assets. They are carried out during planned maintenance and process shutdowns organised according to long-term schedules. A dedicated programme is also employed for automatic control and security systems, providing, among other things, the timeframes for tests and functionality checks. In parallel, the Risk Based Inspection (RBI) programme is being implemented for the Płock facilities in partnership with and under the supervision of the Polish Office of Technical Inspection. The programme offers the added value of continuous improvement of availability and safety of process units with the integrity of production assets maintained. In addition, an Autonomous Plant Maintenance programme is in place, making it possible to achieve a higher level of reliability and safety of production units.
Efforts to counter the COVID-19 pandemic
A number of procedures and information materials related to the COVID-19 pandemic have been developed and implemented in the area of occupational safety of ORLEN Group employees and contractors. These included ‘Recommendations for Contractors on the prevention of SARS-CoV-2 coronavirus infection’, which were prepared and provided to the relevant parties. Work was carried out on preventive measures implemented at the service stations. The Company was involved in the construction of temporary hospitals in Płock and Ostrołęka. The ORLEN Group's Company Fire Brigades jointly developed a comprehensive procedure to be followed in the conditions of the pandemic. PKN ORLEN's Company Fire Brigade also carried out a number of specialist activities relating to preventive measures.
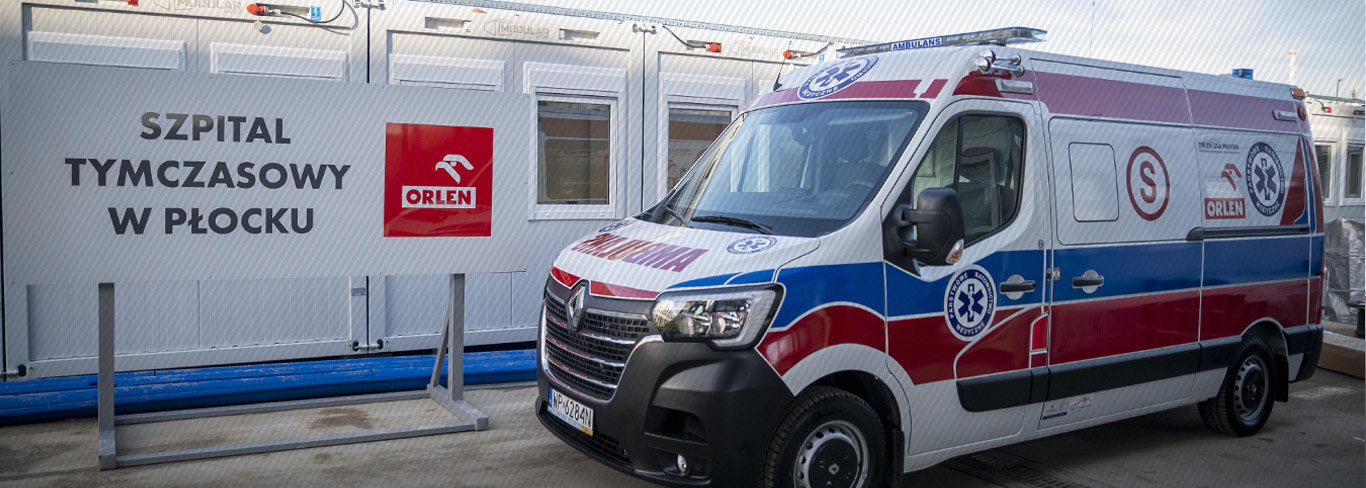
The effects of safety measures undertaken at the ORLEN Group were appreciated by independent expert bodies.
ANWIL as the winner of the ‘Employer – Provider of Safe Work’ competition
The company won the 27th edition of the competition run by the Chief Labour Inspectorate at the regional level. ANWIL was evaluated within the category of employers with a headcount of more than 249. The purpose of the competition is to promote employers which organise work so as to guarantee a high level of employee safety and health protection, and which observe labour law regulations, including those pertaining to the lawfulness of employment. The competition serves to build a positive image of the employers committed to constantly improving their OHS performance.
Silver Cards of Safe Work Leaders for 2021–2022 awarded to ORLEN Laboratorium S.A. and ORLEN Upstream by the Safe Work Leaders Forum at the Central Institute for Labour Protection – National Research Institute (CIOP-PIB) in Warsaw
They have been awarded in recognition of the outcomes of the companies’ efforts to improve working conditions, safety and personal protection in the workplace. They are national awards given to members of the Safe Work Leaders’ Forum in recognition of outstanding efforts designed to promote work safety.
PKN ORLEN received an award in the European Responsible Care Awards competition held by the European Chemical Industry Council (CEFIC)
The awards were presented for inspiring and effective initiatives offered by the Responsible Care Programme Participants across Europe as support during the coronavirus crisis. PKN ORLEN S.A. won the award in the ‘Upholding and Reshaping Production Lines’ category for the production of hand sanitiser liquid at the ORLEN OIL production plant in Jedlicze.
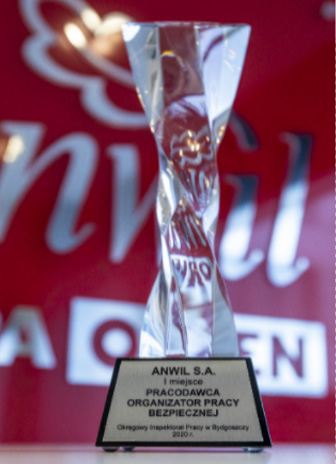
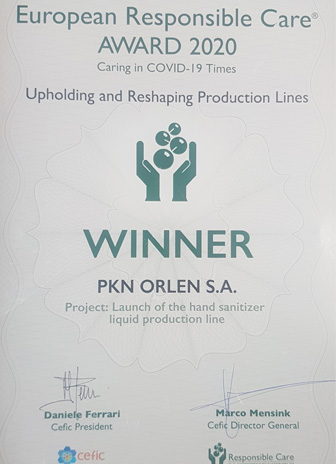
KPIs concerning personaland process safety at the ORLEN Group
TRR
Accident rate (Total Recordable Rate1) |
UoM |
2020 |
2019 |
ORLEN Group |
[number] |
0.72* |
0.90 |
1) Total Recordable Rate = an internationally recognised metric of a company’s rate of workplace accidents calculated as follows: (number of workplace accidents of employees and contractors resulting in working days lost in a period of time / number of man-hours worked by employees and contractors in the period) x 1,000,000.
*Since May 1st 2020, the TRR rate3) has additionally reflected the number of accidents at work involving Energa Group employees. Therefore, in 2020 TRR for ORLEN Group employees was 1.66, which means an increase relative to 1.29 in 2019. In 2020, the Energa Group did not report on components of the Combined Total Recordable Rate for contractors, therefore the Combined TRR for the ORLEN Group including the Energa Group data will be reported starting from 2021.
2) TRR for employees = (number of workplace accidents of employees resulting in working days lost in a period of time / number of man-hours worked by employees in the period) x 1,000,000.
In order to steadily improve the effectiveness of measures fostering a safe work culture, the ORLEN Group has put in place a Safety Culture Indicator, which combines the TRR, a reactive metric, with a proactive element in the form of management of any reported work safety hazards. The Safety Culture Indicator enables monitoring of accident rates and of proactive measures, such as systems for reporting work safety hazards, the purpose of which is to eliminate at source the risk of accidents.
Safety Culture Indicator
Safety Culture Indicator |
UoM |
2020 |
2019 |
ORLEN Group |
% |
100** |
100 |
The Safety Culture Indicator is a sum of:
- the product of the percentage showing achievement of the target for the combined TRR (company and contractors) by a company and 0.7 (accident rate weight in the Safety Culture Indicator),
- the product of the percentage showing achievement of the target for the Risk Notification and Handling Indicator by a company and 0.3 (risk notification weight in the Safety Culture Indicator).
**In 2020, the ENERGA Group did not report on components of the Safety Culture Indicator for contractors and on Work Safety Hazard Reports, therefore this indicator will be reported for the ORLEN Group including the ENERGA Group data starting from 2021.
Accidents at work involving ORLEN Group employees and contractors
GENDER |
ORLEN Group |
|||
2020 |
2019 |
|||
Women |
Men |
Women |
Men |
|
Total number of accidents at work involving employees4) |
4 |
78 |
7 |
41 |
Total number of accidents at work involving contractors5) |
6 |
17 |
16 |
17 |
Total number of accidents at work involving employees and contractors |
10 |
95 |
23 |
58 |
In 2020, the number of accidents at work involving employees of the ORLEN Group increased due to the inclusion, as of May 1st 2020, of the number of accidents at work of the ENERGA Group employees (35 accidents at work involving employees).
REGIONS6) |
ORLEN Group |
|||||||||
2020 |
2019 |
|||||||||
Poland |
Czech Republic |
Lithuania |
Germany |
Canada |
Poland |
Czech Republic |
Lithuania |
Germany |
Canada |
|
Total number of accidents at work involving employees4) |
63 |
15 |
4 |
0 |
0 |
33 |
13 |
0 |
2 |
0 |
Total number of accidents at work involving contractors5) |
17 |
6 |
0 |
0 |
0 |
28 |
4 |
0 |
1 |
0 |
Total number of accidents at work involving employees and contractors |
80 |
21 |
4 |
0 |
0 |
61 |
17 |
0 |
3 |
0 |
4) Number of accidents at work involving ORLEN Group employees which were acknowledged by the employer and were the direct cause of the injured employee’s taking sick leave.
5) Number of acknowledged accidents at work involving employees of the ORLEN Group’s contractors who performed work for a Group company on premises owned or leased by a Group company, which accidents were the direct cause of the injured employee’s taking sick leave. The definition of ‘contractor’ covers also employees of the PKN ORLEN service stations.
6) Regions – markets in which the ORLEN Group has assets.
In 2020, the number of accidents at work involving employees of the ORLEN Group increased due to the inclusion, as of May 1st 2020, of the number of accidents at work of the ENERGA Group employees (35 accidents at work involving employees).
GENDER |
ORLEN Group |
|||
2020 |
2019 |
|||
Women |
Men |
Women |
Men |
|
Number of fatal accidents at work involving employees |
0 |
0 |
0 |
0 |
Number of minor accidents at work involving employees |
4 |
78 |
7 |
41 |
Total number of accidents at work involving employees |
4 |
78 |
7 |
41 |
REGIONS6) |
ORLEN Group |
|||||||||
2020 |
2019 |
|||||||||
Poland |
Czech Republic |
Lithuania |
Germany |
Canada |
Poland |
Czech Republic |
Lithuania |
Germany |
Canada |
|
Number of fatal accidents at work involving employees |
0 |
0 |
0 |
0 |
0 |
0 |
0 |
0 |
0 |
0 |
Number of minor accidents at work involving employees |
63 |
15 |
4 |
0 |
0 |
33 |
13 |
0 |
2 |
0 |
Total number of accidents at work involving employees |
63 |
15 |
4 |
0 |
0 |
33 |
13 |
0 |
2 |
0 |
6) Regions – markets in which the ORLEN Group has assets
In 2020, all accidents at work involving ORLEN Group employees were minor accidents, just like in 2019. In 2020, the Group reported one collective accident at work (the ORLEN Unipetrol Group), vs. none in 2019.
GENDER |
Grupa ORLEN |
|||
2020 |
2019 |
|||
Women |
Men |
Women |
Men |
|
Number of fatal accidents at work involving contractors |
0 |
0 |
0 |
0 |
Number of minor accidents at work involving contractors |
6 |
17 |
16 |
17 |
Total number of accidents at work involving contractors |
6 |
17 |
16 |
17 |
REGIONS6) |
ORLEN Group |
|||||||||
2020 |
2019 |
|||||||||
Poland |
Czech Republic |
Lithuania |
Germany |
Canada |
Poland |
Czech Republic |
Lithuania |
Germany |
Canada |
|
Number of fatal accidents at work involving contractors |
0 |
0 |
0 |
0 |
0 |
0 |
0 |
0 |
0 |
0 |
Number of minor accidents at work involving contractors |
17 |
6 |
0 |
0 |
0 |
28 |
4 |
0 |
1 |
0 |
Total number of accidents at work involving contractors |
17 |
6 |
0 |
0 |
0 |
28 |
4 |
0 |
1 |
0 |
6) Regions – markets in which the ORLEN Group has assets
In 2020, all accidents at work involving ORLEN Group contractors were minor accidents, just like in 2019. In 2020 and 2019, there were no collective accidents at work involving contractors within the Group.
Accidents at work involving employees of the ORLEN Group, by type of injury
TYPE OF INJURY |
UoM |
ORLEN Group |
|
2020 |
2019 |
||
cuts |
[%] |
20.48 |
18.75 |
bruises |
15.66 |
16.67 |
|
burns |
13.25 |
10.42 |
|
fractures |
10.84 |
14.58 |
|
dislocations and sprains |
32.53 |
25.00 |
|
Other |
7.23 |
14.58 |
Accidents at work involving contractors of the ORLEN Group, by type of injury
TYPE OF INJURY |
UoM |
ORLEN Group |
|
2020 |
2019 |
||
cuts |
[%] |
26.09 |
12.12 |
bruises |
21.74 |
12.12 |
|
burns |
4.35 |
9.09 |
|
fractures |
30.43 |
15.15 |
|
dislocations and sprains |
13.04 |
24.24 |
|
other |
4.35 |
27.27 |
Accidents at work involving employees of the ORLEN Group, by type of activity
TYPE OF INJURY |
UoM |
ORLEN Group |
|
2020 |
2019 |
||
day-to-day operation of plant and equipment |
[%] |
20.73 |
25.00 |
movement |
40.24 |
41.67 |
|
plant engineering, maintenance and repairs |
23.17 |
14.58 |
|
road collisions |
7.32 |
6.25 |
|
other activities |
8.54 |
12.50 |
Accidents at work involving contractors of the ORLEN Group, by type of activity
TYPE OF INJURY |
UoM |
Grupa ORLEN |
|
2020 |
2019 |
||
day-to-day operation of plant and equipment |
[%] |
8.70 |
6.06 |
movement |
17.39 |
18.18 |
|
plant engineering, maintenance and repairs |
8.70 |
18.18 |
|
road collisions |
8.70 |
0.00 |
|
other activities |
56.52 |
57.58 |
TRR for ORLEN Group employees 3)
GENDER |
ORLEN Group |
||
Total |
Women |
Men |
|
2020 |
1.66 |
0.30 |
2.15 |
2019 |
1.29 |
0.70 |
1.51 |
REGIONS6) |
ORLEN Group |
|||||
Total |
Poland |
Czech Republic |
Lithuania |
Germany |
Canada |
|
2020 |
1.66 |
1.67 |
1.84 |
1.22 |
0 |
0 |
2019 |
1.29 |
1.35 |
1.47 |
0.00 |
6.48 |
0.00 |
3) Total number of accidents at work involving employees of ORLEN Group companies and resulting in the injured person taking sick leave in a given period x 1,000,000 / number of man-hours worked by the employees in this period.
6) Regions – markets in which the ORLEN Group has assets.
The increase in the TRR rate for ORLEN Group employees relative to 2019 is attributable to the inclusion, starting from May 1st 2020, of the number of accidents at work involving employees of the ENERGA Group.
Severity rates7) for accidents at work involving ORLEN Group employees in 2020
GENDER |
ORLEN Group |
||
Total |
Women |
Men |
|
2020 |
43.22 |
97.25 |
40.45 |
REGIONS6) |
ORLEN Group |
|||||
Total |
Poland |
Czech Republic |
Lithuania |
Germany |
Canada |
|
2020 |
43.22 |
41.95 |
44.00 |
60.25 |
0 |
0 |
6) Regions – markets in which the ORLEN Group has assets.
7) Quotient of the number of days lost due to post-accident absenteeism of ORLEN Group employees and the number of accidents at work involving ORLEN Group employees, acknowledged by the employer and resulting in the employee's taking sick leave.
Number of days lost due to post-accident absenteeism8) at the ORLEN Group in 2020
GENDER |
ORLEN Group |
||
Total |
Women |
Men |
|
2020 |
3,544 |
389 |
3,155 |
REGIONS6) |
ORLEN Group |
|||||
Total |
Poland |
Czech Republic |
Lithuania |
Germany |
Canada |
|
2020 |
3,544 |
2,643 |
660 |
241 |
0 |
0 |
6) Regions – markets in which the ORLEN Group has assets.
8) Number of days on which ORLEN Group companies’ employees were on sick leaves in a given period as a result of an accident at work acknowledged by the employer.
Ensuring work safety and health protection for employees of external contractors performing work on the ORLEN Group premises is one of the Group’s priorities. In order to continuously enhance their safety we have taken a consistent, long-term approach to raising their awareness of the importance of proper risk assessment, potential hazards, risk mitigation methods, OHS rules and procedures, proper use of protective systems and equipment, and the need to report potentially dangerous situations. Besides analysing work accidents suffered by contractors, the ORLEN Group also studies data on sick leaves resulting from the accidents occurring in connection with work carried out by contractors on the premises of Group companies.
However, the Group is not legally authorised to publish such data.
Number of occupational disease cases in each employee Group9)
EMPLOYEE GROUPS |
ORLEN Group |
|
2020 |
2019 |
|
Office and administrative staff |
0 |
0 |
Higher-rank and mid-level technical staff |
0 |
0 |
Operators of process units and equipment |
1 |
2 |
Repair and maintenance employees |
2 |
2 |
Transport and storage employees |
0 |
1 |
Total
|
3* |
5** |
9) Number of acknowledged occupational disease cases is the number of decisions issued by the State Sanitary Inspector to confirm recognition of an occupational disease of a current or former employee of an ORLEN Group company.
* ORLEN Lietuva (2), ORLEN Unipetrol Group (1)
**ORLEN Lietuva (5)
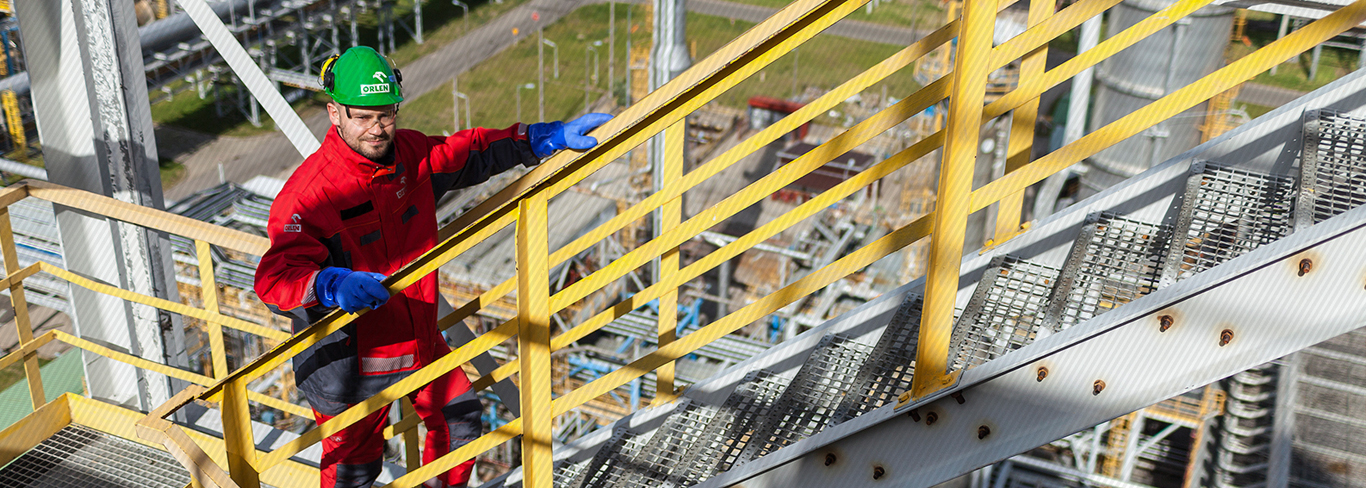
In 2019, the occupational diseases were caused by factors related to lifting and handling, exposure to chemical agents, noise, mechanical dislocations, and poor working posture. In 2020, they were associated with lifting and handling, noise and work with hazardous materials; employees suffered from: a spinal disease, hearing injury and respiratory disease.
The ORLEN Group does not report on the incidence of occupational diseases of contractors’ employees due to the absence of tools or legal regulations that would enable obligating third parties to report such cases, which is also the case with information on third party and ORLEN Group employee deaths from occupational diseases.
Workers with high incidence or high risk of occupational diseases
The ORLEN Group constantly monitors and identifies factors that may cause occupational diseases among its employees. Work environment surveys are performed on a regular basis and their results are analysed to assess the risk of potential impact on the health of the Group’s employees. With respect to all factors identified for jobs with a high risk of occupational disease, systemic preventive measures have been implemented in the form of technical and organisational solutions offering personal and collective protection. The use of such solutions eliminates the risk of employees developing occupational diseases as a result of harmful factors in their work environment.
In consequence, the incidence of occupational diseases involving ORLEN Group employees in 2019–2020 was lower.
ProcessSafety
Process Safety Management System
Process safety is becoming a specific field related to resilience engineering, which defines safety as the ability to maintain plant success under normal and emergency conditions. Another noteworthy aspect is organisational systems capable of an immediate response to maintain business continuity. Twenty nine establishments at the ORLEN Group are classified as upper-tier, and a number almost half of that are lower-tier establishments, as per the classification framework under the Seveso III Directive applicable across Europe and implemented into national law by all EU member states in 2015. In Poland, the relevant regulations are laid down in the Environmental Protection Law. The establishments of both types have in place modern and constantly improved process safety management systems as an organised method for managing safety, encompassing all the vital safety components referred to above.
T1 PSER (Process Safety Events Rate1) |
UoM |
2020 |
2019 |
ORLEN Group |
[number] |
0.05 |
0.09 |
1) Tier 1 Process Safety Events Rate = number of process safety events according to API 754 (number of events of greater consequence related to substance release into the environment / number of man-hours) x 1,000,000
ORLEN Group facilities with a high and increased risk of a major accident
POLAND |
||
PKN ORLEN |
7 upper-tier establishments |
10 lower-tier establishments |
ORLEN PALIWA |
6 upper-tier establishments |
1 lower-tier establishments |
BOP |
1 upper-tier establishment |
--- |
ANWIL |
1 upper-tier establishment |
--- |
ORLEN Południe |
2 upper-tier establishment |
--- |
ORLEN Aviation |
--- |
1 lower-tier establishmentt |
IKS 'Solino' |
1 upper-tier establishment |
--- |
CZECH REPUBLIC |
||
ORLEN Unipetrol RPA |
3 upper-tier establishment |
--- |
ORLEN Unipetrol DOPRAVA |
5 upper-tier establishment |
--- |
PARAMO |
1 upper-tier establishment |
--- |
SPOLANA |
1 upper-tier establishment |
--- |
LITHUANIA |
||
ORLEN Lietuva |
2 upper-tier establishments |
--- |
To describe the current status of process safety at the ORLEN Group production companies, the Group uses various process safety indicators, including leading and lagging ones, in accordance with the API 754 standards. Those indicators are monitored and measured using the Company’s internal application to help achieve the overarching objective of process safety management, which means preventing and minimising the risk of major accidents. These indicators also serve as the basis for benchmarking against the best companies in the industry and thus contribute to achieving process excellence.
Number of process safety eventsby business activity
TIER 1, TIER 2 and TIER 3 emergencies
TIER 1 emergencies
These are emergencies with a significant impact related to a sudden and unexpected substance release due to ineffective protection layers. Such emergencies include a sudden and unexpected release of hazardous substances or non-toxic and non-flammable substances (steam, condensate, hot water, nitrogen, compressed air, CO2) during ongoing industrial processes, having one or more of the following consequences:
- injury to an employee of the ORLEN Group or of a contractor or subcontractor, resulting in a sick leave or death;
- hospital admission and/or death of any other person;
- officially announced evacuation of local residents or recommendation for them not to leave their homes;
- fire or explosion resulting in losses in the form of direct costs of at least USD 100 thousand (USD 100,000 x ~3 PLN/USD = ~PLN 300,000);
- release of excessive pressure into the atmosphere with the use of pressure relief devices in an amount equal to or higher than the threshold amount in any one hour period;
- release of a substance in an amount equal to or higher than the threshold amount in any one hour period.
TIER 2 emergencies
These are events of lesser consequence related to a sudden and unexpected substance release due to ineffective protection layers. Such emergencies include a sudden and unexpected release of hazardous substances or non-toxic and non-flammable substances (steam, condensate, hot water, nitrogen, compressed air, CO2) during ongoing industrial processes, having one or more consequences not classified as TIER1, including:
- injury to an employee of the ORLEN Group or of a contractor or subcontractor;
- fire or explosion resulting in losses in the form of direct costs of at least USD 2,500 (USD 2,500 x ~3 PLN/USD = ~PLN 7,500);
- release of excessive pressure into the atmosphere in an amount equal to or higher than the threshold TIER2 amount in any one-hour period;
- release of a substance in an amount equal to or higher than the threshold TIER2 amount in any one-hour period.
Number of TIER 1, TIER 2 and TIER 3 emergencies
The indicators do not include the Energa Group. Energa Group data will be included in the ORLEN Group's statistics as of 2021.
In 2020, the ORLEN Group continued reporting the T3 (TIER 31) process safety indicator referring to near-miss events.
1It has been assumed that TIER 3 emergencies are emergency shutdowns of installations or process nodes triggered by active or passive protections (automatic or mechanical). TIER3 ratio is calculated as follows:
- TIER 3 production emergencies – number of emergency shutdowns of installations or process nodes triggered by active or passive protections (automatic or mechanical);
- TIER 3 logistics emergencies – ratio of the number of emergency shutdowns of product loading to rail tank cars and road tankers triggered by active or passive protections (automatic or mechanical) to the total number of loading operations performed at a given time.
Number of emergencies at the ORLEN Group |
2020 |
||
Poland |
Czech Republic |
Lithuania |
|
TIER 1 |
1 |
4 |
0 |
TIER 2 |
1 |
6 |
1 |
TIER 3 - Production |
87 |
0 |
16 |
Number of emergencies at the ORLEN Group |
2019 |
||
Poland |
Czech Republic |
Lithuania |
|
TIER 1 |
0 |
7 |
1 |
TIER 2 |
2 |
2 |
0 |
TIER 3 - Production |
59 |
1 |
10 |
T1 PSER1 and T2 PSER2:
The indicators do not include the Energa Group. Energa Group data will be included in the ORLEN Group's statistics as of 2021.
TIER 1 and TIER 2 events reported for 2020 involved only emissions into the environment caused by fires and leaks. There were no emergencies causing serious damage to the natural environment. Liquid leaks were collected and properly disposed of.
2T1 PSER = (number of TIER 1 emergencies, of greater consequence, related to substance release into the environment/ number of man-hours worked by employees and contractors) x 1,000,000.
2T2 PSER = (number of TIER 2 emergencies, of lesser consequence, related to substance release into the environment/number of man-hours worked by employees and contractors) x 1,000,000.
Total number and volumeof significant spills
Total number and volume of significant spills in 2020 was as follows:
- Number of spills in 2020 – 8 (2019: 10)
-
Volume of spills in 2020 – ca. 31 Mg (2019: approximately 140 Mg)
Information on each spill reported by ORLEN Group companies in 2020 is presented in the table below.
No. |
Location |
Volume [Mg] |
Type of substance |
Comment |
1. |
ORLEN Unipetrol RPA Production plant in Kralupy, storage tank park |
approx. 0.5 |
Fuel spill (reformed gasoline) |
On the unit’s site; no impact on soil or water surface |
2. |
PKN ORLEN Fuel Terminal in Widełka, road tanker loading front |
approx. 0.5 |
Fuel spill (diesel oil) |
On the unit’s site; no impact on soil or water surface |
3. |
PKN ORLEN Fuel Terminal in Lublin, OPB unit |
approx. 5 |
Fuel spill (motor gasoline ES95) |
On the unit’s site; no impact on soil or water surface |
4. |
ORLEN Unipetrol RPA Production plant in Litvínov, steam cracker |
approx. 0.18 |
Spill of chemicals (benzene) |
On the unit’s site; no impact on soil or water surface |
5. |
ORLEN Lietuva Production plant in Mažeikiai, elemental sulfur unit |
approx. 0.49 |
Spill of chemicals (elemental sulphur) |
On the unit’s site; no impact on soil or water surface |
6. |
SPOLANA Production plant in Neratowice, rail tank car unloading front |
approx. 23 |
Spill of chemicals (33% HCl solution) |
On the unit’s site and partial release into the atmosphere; no impact on soil or water surface |
7. |
ORLEN Unipetrol Production plant in Litvínov, NH3 loading station |
approx. 1.1 |
Spill of chemicals (ammonia) |
On the unit’s site and partial release into the atmosphere; no impact on soil or water surface |
8. |
ORLEN Unipetrol RPA Litvínov production plant, railway track 234 |
approx. 0.27 |
Spill of chemicals (isobutane) |
Release into the atmosphere; no impact on soil or water surface |
Most of those spills involved contamination of equipment and the unit sites, without any impact on soil or water surface. In addition, most of those incidents required covering the costs of rescue operations by Company Fire Brigades as well as repair or replacement of damaged equipment. Two cases of partial release of gaseous substances into the atmosphere were reported. Four employees of ORLEN Group companies were injured as a result (three of them inhaled gas vapour, one suffered a burn injury). All of them were provided with on-site medical assistance, in two cases the employees were hospitalised.
Description of significant risks in the area of Occupational Health and Safety and the methods of managing these risks can be found in the ‘Report on non-financial information of the ORLEN Group and PKN ORLEN S.A.’